Lunar Spaceport Architectures
Lunar spaceport applied design theoryclient: Open Lunar Foundation
myrole/scope: author and designer
type: Part time fellowship
paper exerpt:Introduction
Lunar spaceports (a.k.a.. launch/ landing pads) will be a cornerstone of all but the most anemic lunar futures. Undoubtedly, they are critical to any sustainable presence. The central problem spaceports address is the detrimental effects of ejecta, the dispersal of lunar surface material (rocks, dust, etc.), caused by landing on and launching atop unprotected lunar ground. The Moon has no atmosphere so ejecta goes fast and far, potentially blanketing the globe at velocities that could damage infrastructure and undermine science and reaching altitudes where satellites and orbital habitats dwell.
Consistent with this values of Open Lunar Foundation, this is a working document for designers, engineers, and policy-makers interested in understanding this problem or applying the approach to other problems.
an engineering trade study, nor is it based on previously unpublished information, not is it intended as a set of ready-made designs to choose from.
It is an architectural and conceptual exploration through geometry, mechanism, and concept of operation.
Fig. 1: Stages of rocket exhaust ejecta beneath an Apollo Lunar Module (Metzger et al., 2011).
...Introduction
Lunar spaceports (a.k.a.. launch/ landing pads) will be a cornerstone of all but the most anemic lunar futures. Undoubtedly, they are critical to any sustainable presence. The central problem spaceports address is the detrimental effects of ejecta, the dispersal of lunar surface material (rocks, dust, etc.), caused by landing on and launching atop unprotected lunar ground. The Moon has no atmosphere so ejecta goes fast and far, potentially blanketing the globe at velocities that could damage infrastructure and undermine science and reaching altitudes where satellites and orbital habitats dwell. Consistent with this values of Open Lunar Foundation, this is a working document for designers, engineers, and policy-makers interested in understanding this problem or applying the approach to other problems.
an engineering trade study, nor is it based on previously unpublished information, not is it intended as a set of ready-made designs to choose from.
It is an architectural and conceptual exploration through geometry, mechanism, and concept of operation.
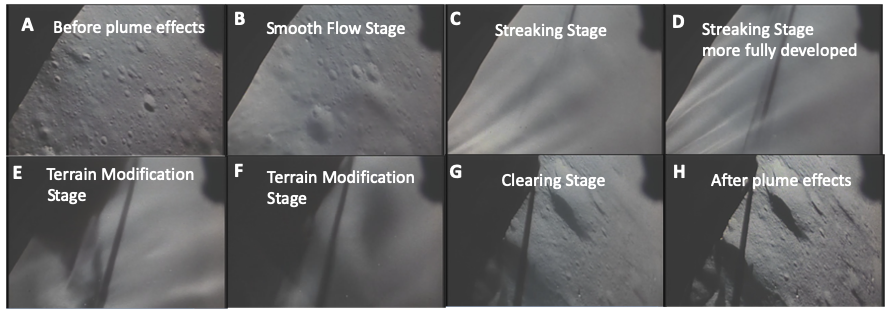
To continue reading the text, click here.
To see the patent-inspired drawings, see below.
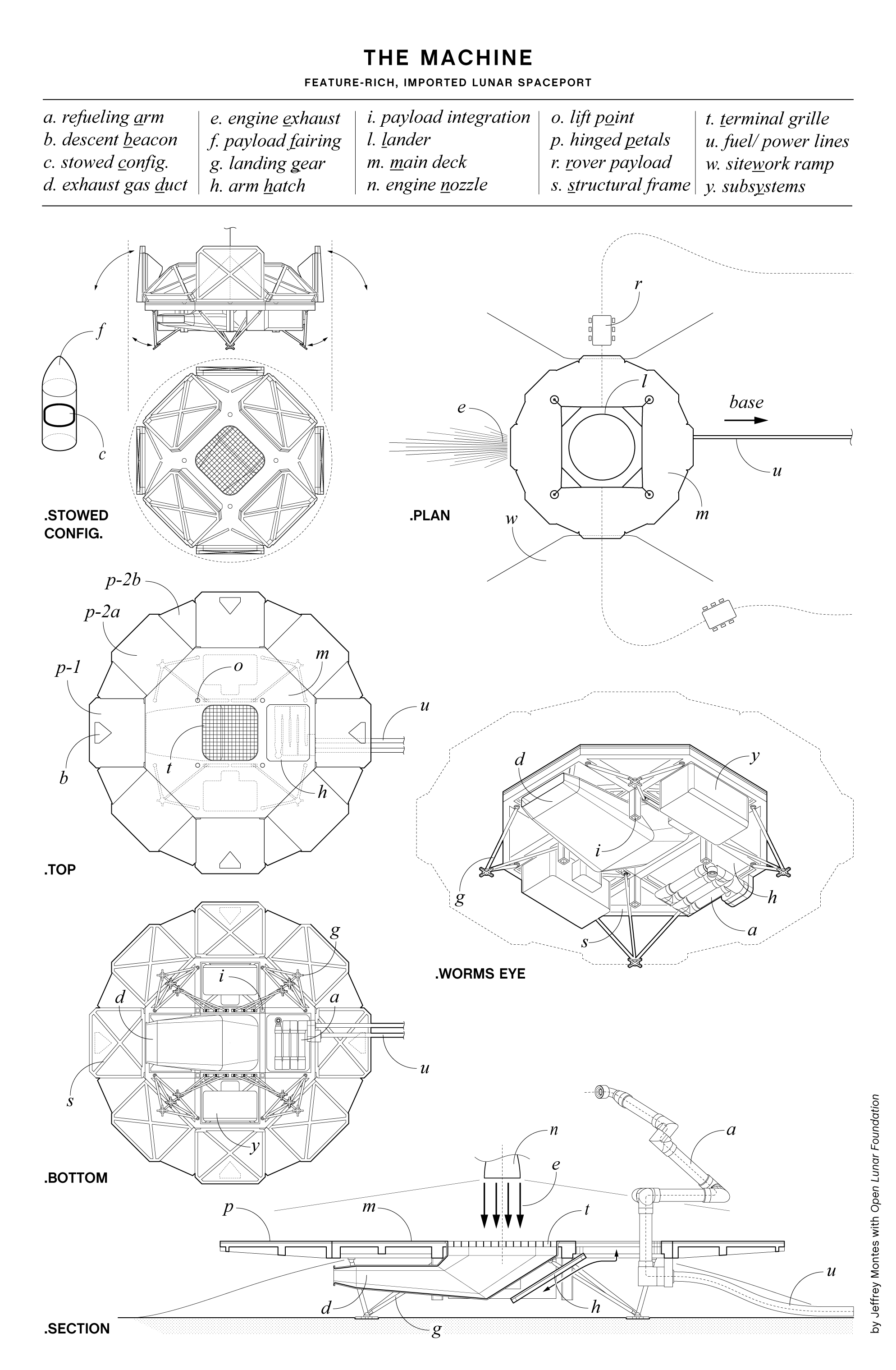
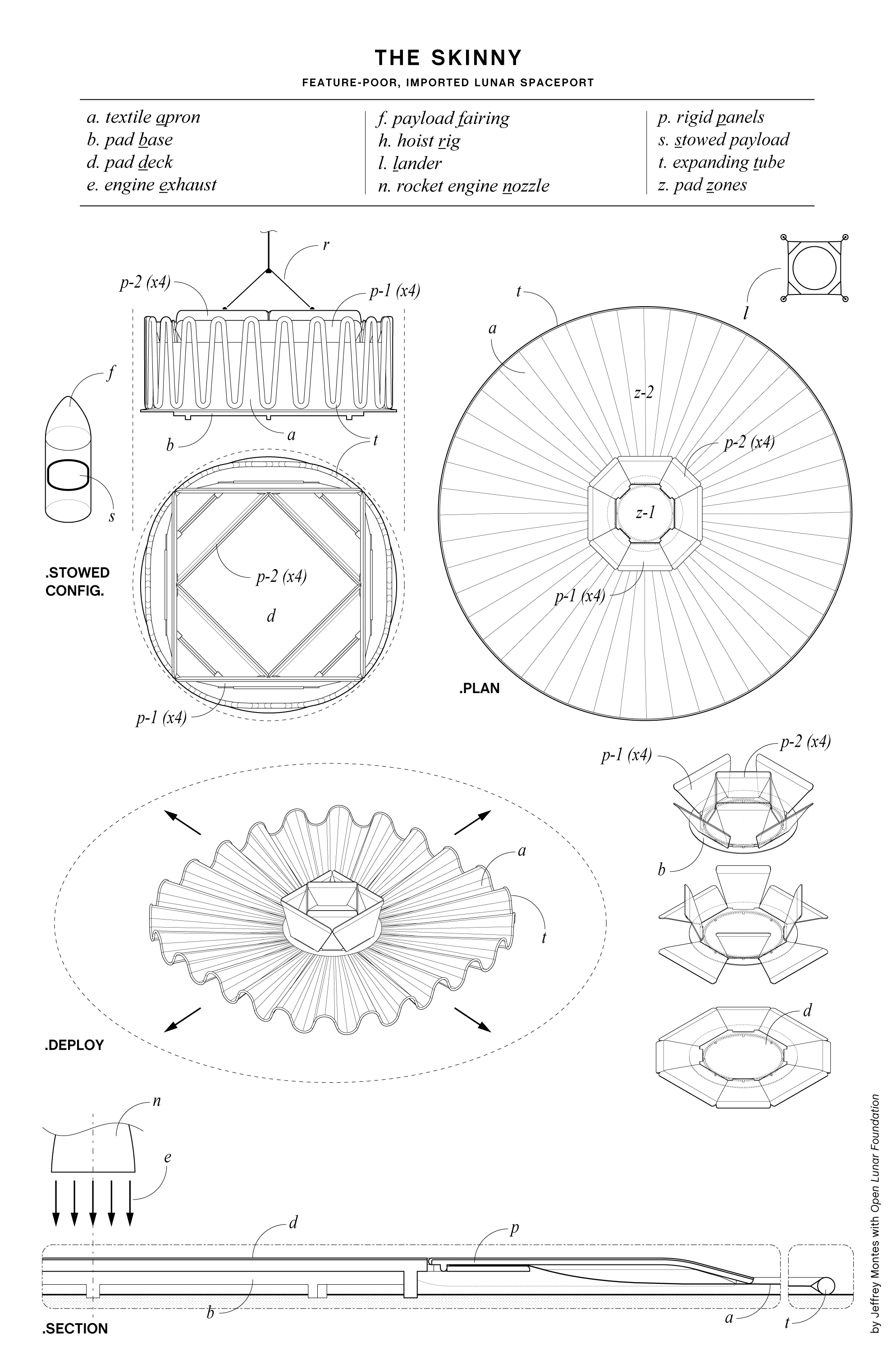
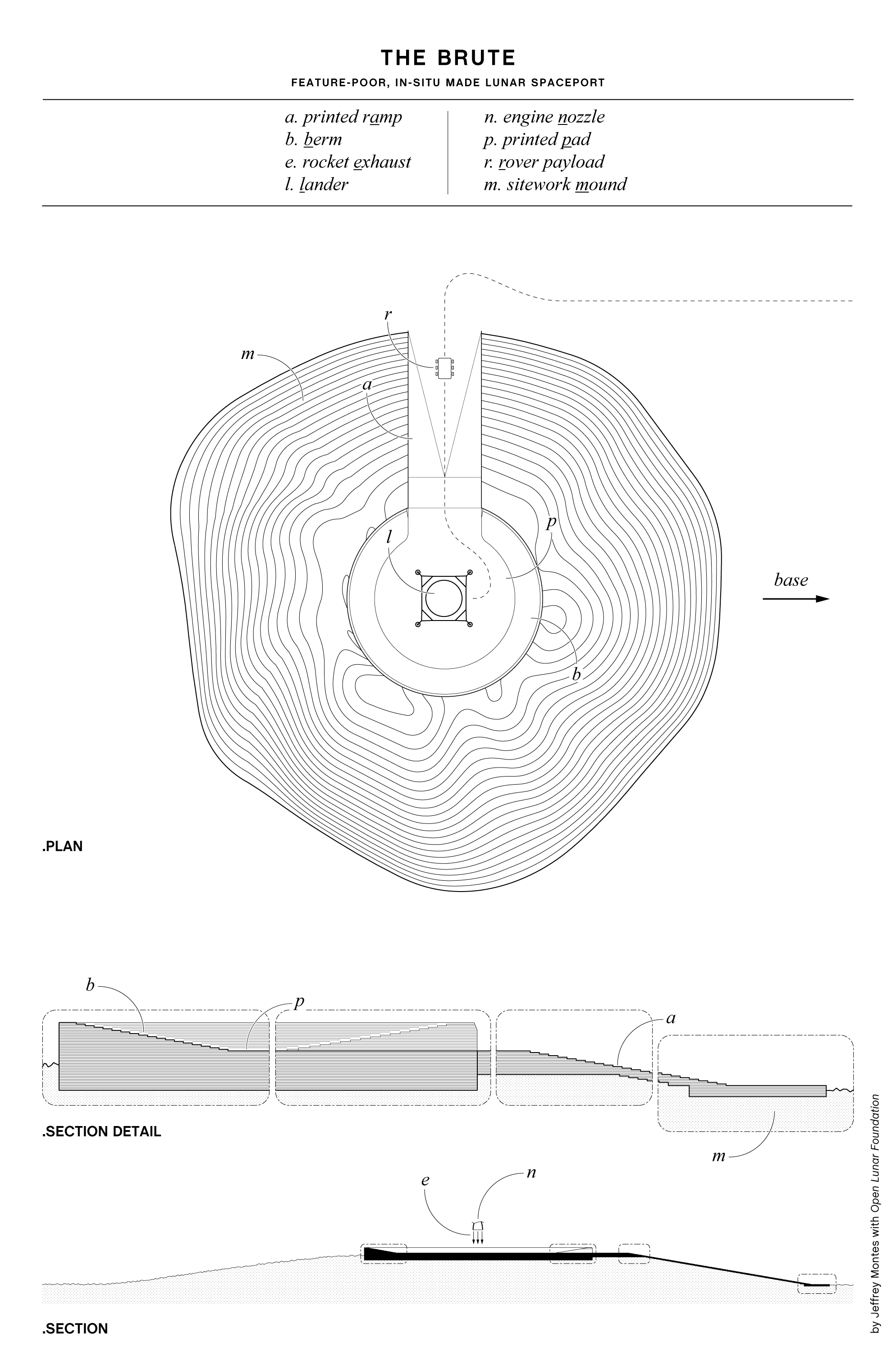
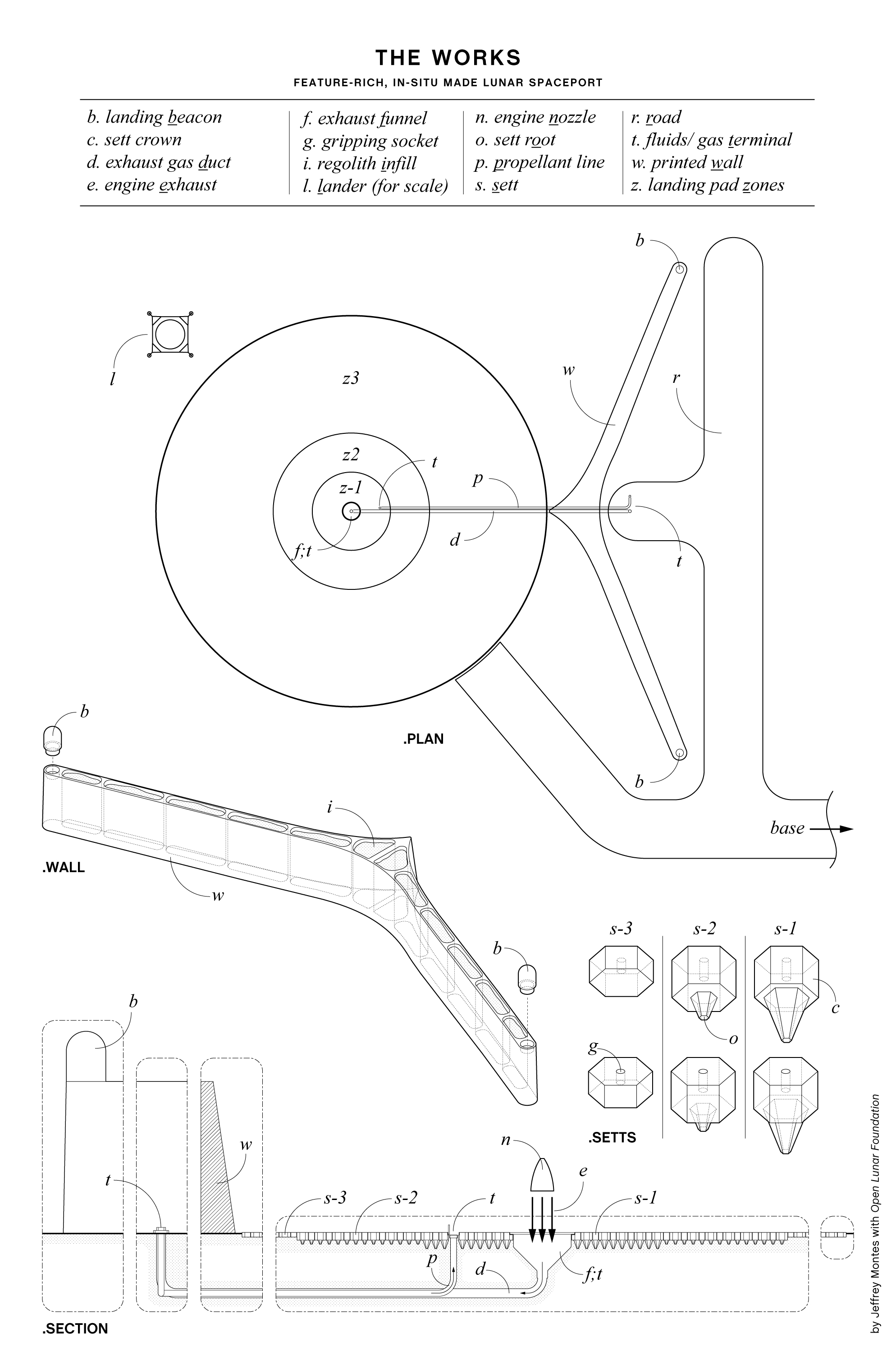