Blue Origin
Senior Space Architect & Design Studio founderclient: various
my role/scope: Senior Space Architect
type: full time
I’ve led or contributed to numerous programs, projects, and studies covering orbital habitats, lunar habitats, space transportation, and lunar surface mobility and infrastructure.
Of those, Orbital Reef, a commercial Space station, is the only one in the public record. Orbital Reef started as a <10 person concept team considering various dissimilar approaches to a station. Since these early stages, I’ve architected and championed a bold and implementable design vision. Years of iteration and research has made me a world expert in the architecture of Space stations.
As defined by the American Institute of Aeronautics and Astronautics, Space architecture is the theory and practice of designing and building inhabited environments for use in Space. I work with systems engineers, system architects, and subject matter experts in all spaceflight subsystems including environmental control and life support, pressure vessels, and interfaces. I'm involved in product strategy, conops development, habitation ecosystem design, architecting of habitable elements, and the design of associated systems and subsystems. My position as an architect of extreme engineering in extreme environments requires pragmatic idealism, curiosity, adaptability, resilience, and informed naivete. My role is equal parts creating archietctural designs and building a culture that can accomplish it.
As Blue Origin’s first designer hired to work on spacecraft design, I am the lead advocate for the formation of an internal design studio to meet our moment of commercial and accessible human spaceflight.
For public release images
Lunar Spaceport Architectures
Lunar spaceport applied design theoryclient: Open Lunar Foundation
myrole/scope: author and designer
type: Part time fellowship
paper exerpt:Introduction
Lunar spaceports (a.k.a.. launch/ landing pads) will be a cornerstone of all but the most anemic lunar futures. Undoubtedly, they are critical to any sustainable presence. The central problem spaceports address is the detrimental effects of ejecta, the dispersal of lunar surface material (rocks, dust, etc.), caused by landing on and launching atop unprotected lunar ground. The Moon has no atmosphere so ejecta goes fast and far, potentially blanketing the globe at velocities that could damage infrastructure and undermine science and reaching altitudes where satellites and orbital habitats dwell.
Consistent with this values of Open Lunar Foundation, this is a working document for designers, engineers, and policy-makers interested in understanding this problem or applying the approach to other problems.
an engineering trade study, nor is it based on previously unpublished information, not is it intended as a set of ready-made designs to choose from.
It is an architectural and conceptual exploration through geometry, mechanism, and concept of operation.
Fig. 1: Stages of rocket exhaust ejecta beneath an Apollo Lunar Module (Metzger et al., 2011).
...Introduction
Lunar spaceports (a.k.a.. launch/ landing pads) will be a cornerstone of all but the most anemic lunar futures. Undoubtedly, they are critical to any sustainable presence. The central problem spaceports address is the detrimental effects of ejecta, the dispersal of lunar surface material (rocks, dust, etc.), caused by landing on and launching atop unprotected lunar ground. The Moon has no atmosphere so ejecta goes fast and far, potentially blanketing the globe at velocities that could damage infrastructure and undermine science and reaching altitudes where satellites and orbital habitats dwell. Consistent with this values of Open Lunar Foundation, this is a working document for designers, engineers, and policy-makers interested in understanding this problem or applying the approach to other problems.
an engineering trade study, nor is it based on previously unpublished information, not is it intended as a set of ready-made designs to choose from.
It is an architectural and conceptual exploration through geometry, mechanism, and concept of operation.
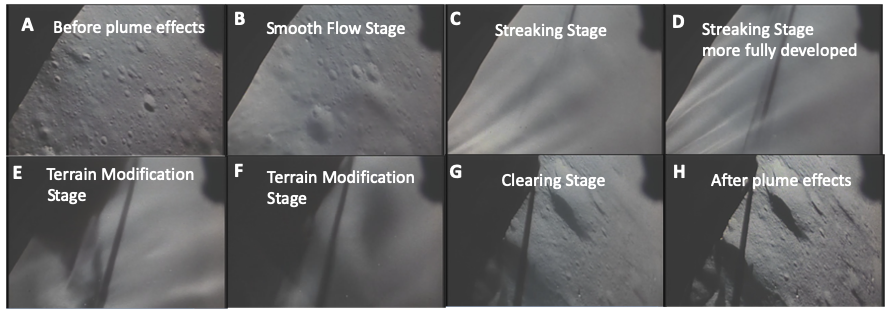
To continue reading the text, click here.
To see the patent-inspired drawings, see below.
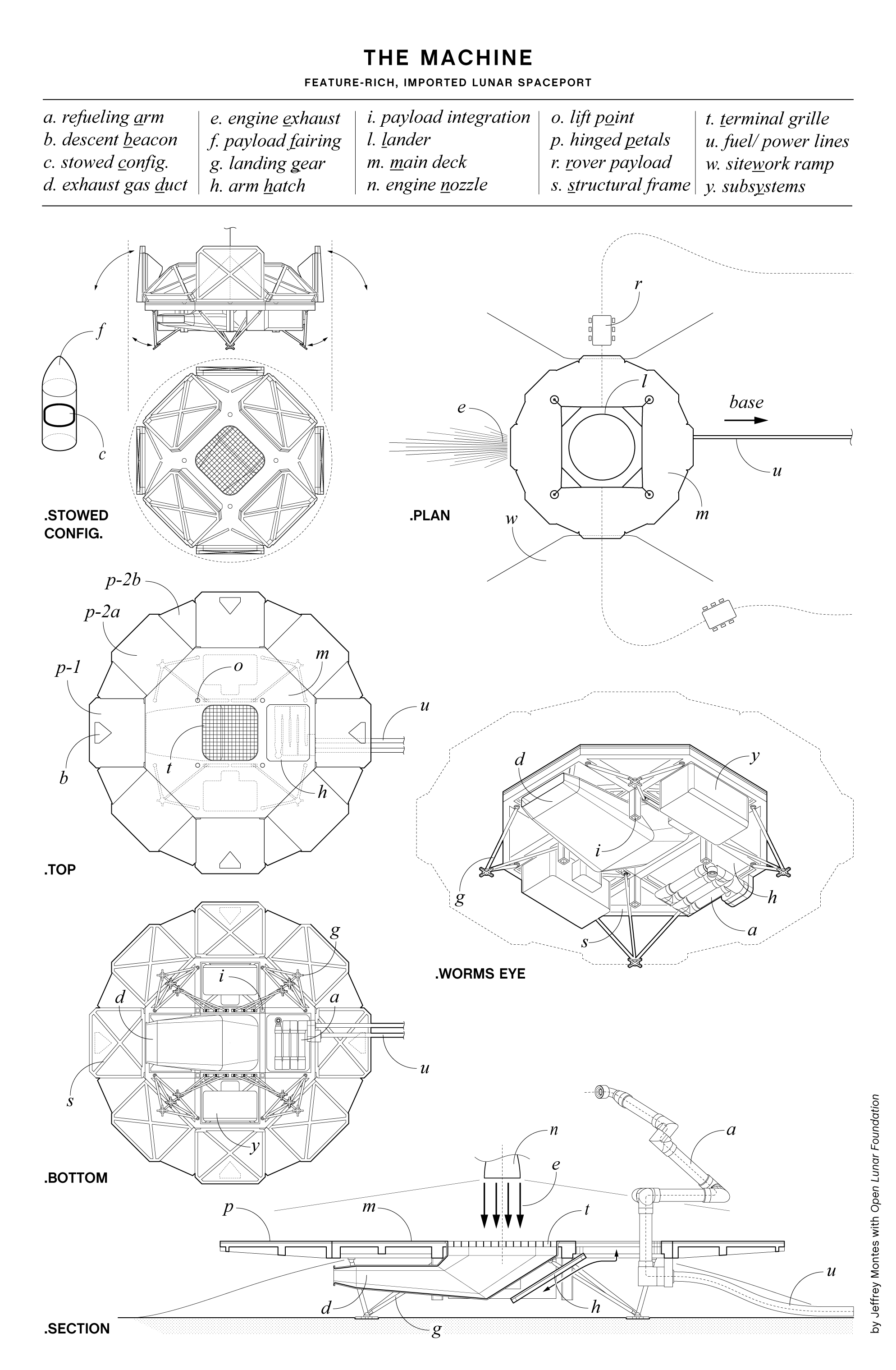
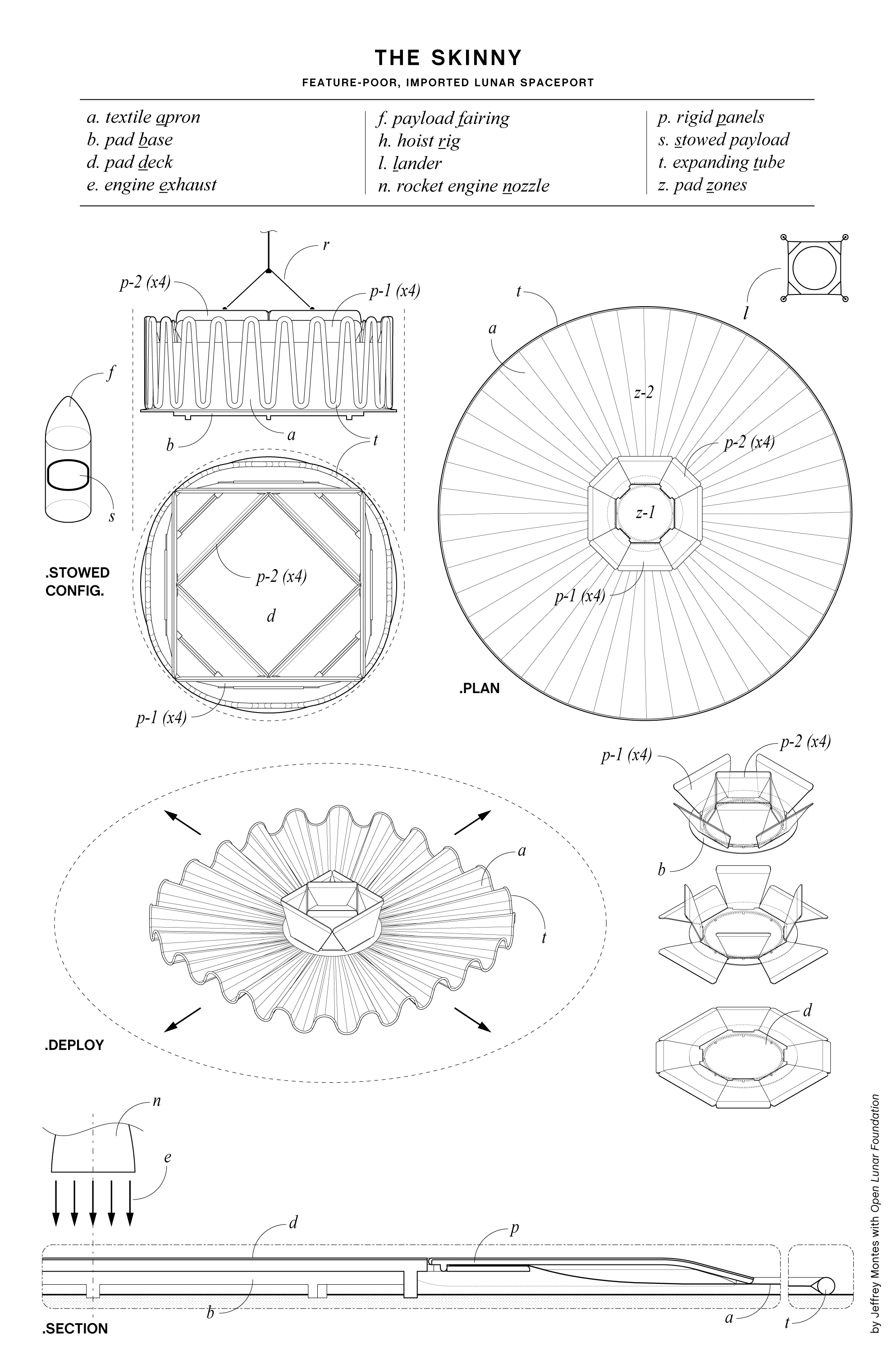
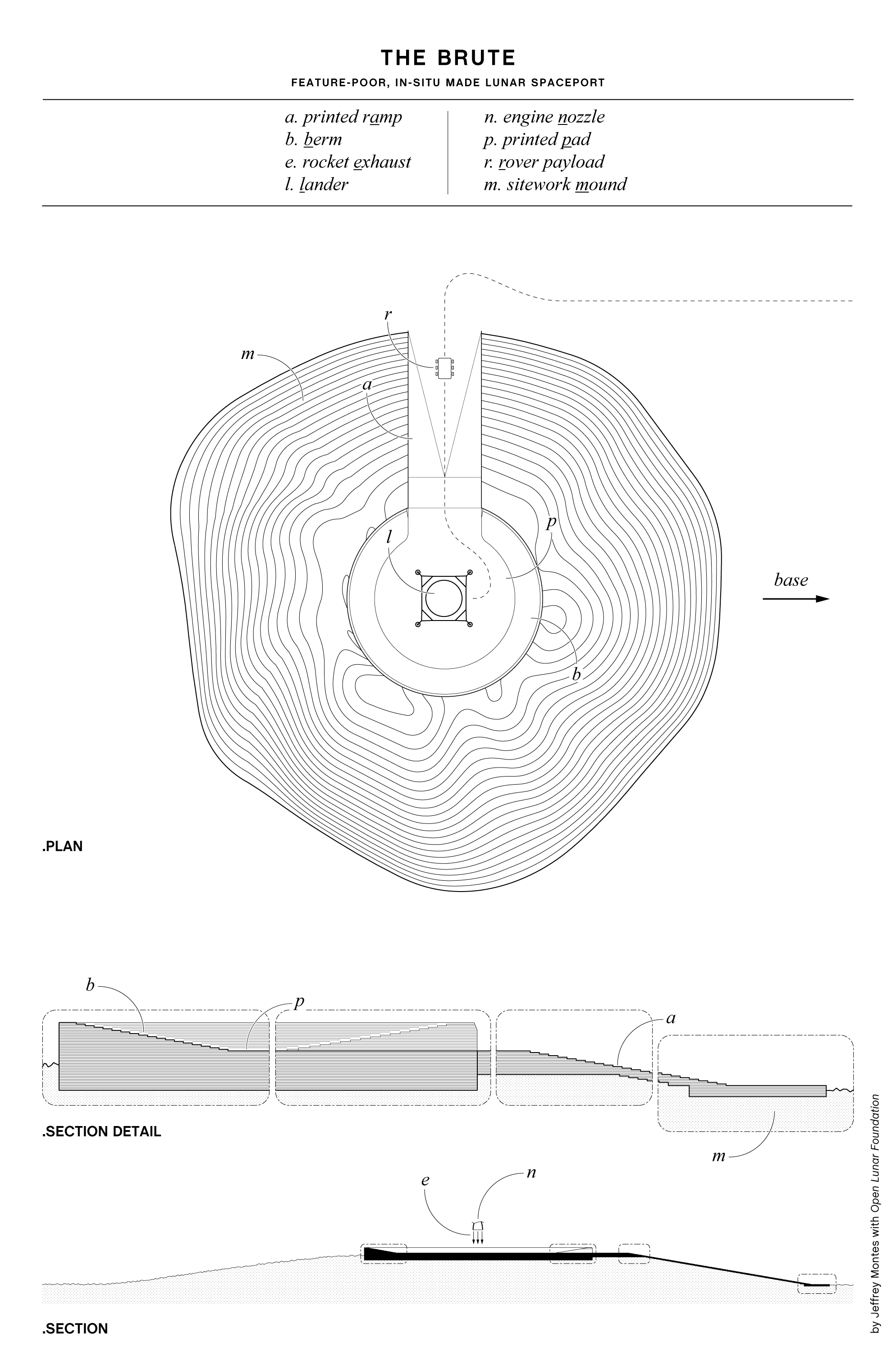
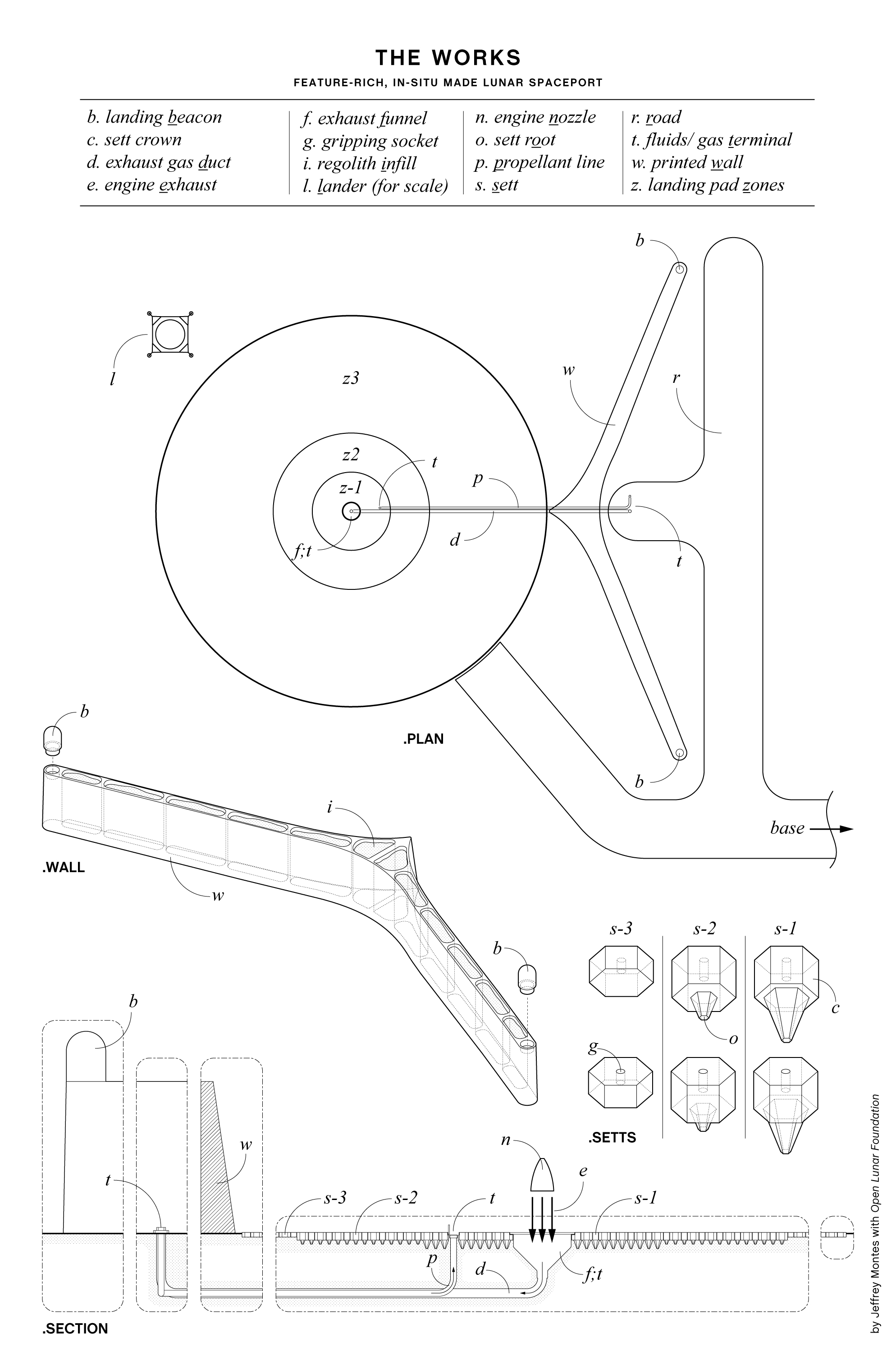
Marsha
Grand prize-winning 3D printed Martian habitat concept and 1:3 scale prototypeclient: NASA
myrole/scope: principal designer and team lead
type: Full time (AI SpaceFactory)
myrole/scope: principal designer and team lead
type: Full time (AI SpaceFactory)
Marsha is a first-principles rethinking of what a Martian habitat could be – not another low-lying dome or confined half-buried structure but a flexible, multi-level, corridor-free home flooded with diffuse natural light and 3D printed using Martian resources. It is born of a careful response to the Martian environment and a synergy between architectural, structural and construction principles with the crew’s experience at the center. Missions present stresses and challenges that can’t be solved at the operational level and must be addressed spatially. Marsha addresses these issues and more, marking a radical departure from prior habitat schemes.
A vertically oriented cylinder is the best formal basis for a surface habitat. It is the most effective way to reduce loading and maximize usable space since it allows usable space to be aggregated vertically with vertical walls and a compact footprint, keep hoop stress and uplift forces manageable.
This configuration lends itself well to joining and separating mission activities in a meaningful way by level, avoiding the need to divide one large area into many small, confined spaces. In the context of additive manufacturing, vertical cylinders are also inherently the most construct-able shape. Inside, a “double shell” system separates the architectural space from the pressure vessel subject to external conditions, allowing the interior to be high mass-optimized to serve the creation of habitable spaces. The space between the two serves multiple uses including natural daylighting, circulation and maintenance access.
![]()
The first towards construction of a prototype was the formulation of a construction material. At our direction Techmer PM formulated a high-performance “Martian polymer”: a basalt fiber-reinforced polylactic acid. This material was novel in that it used a “biopolymer” that can be made from plants high in polysaccarides (sugars) combined with volvanic rock that is known to be relatively abundant on Mars (and the Moon). Eventually, humanity will leverage in-situ resource utilization (ISRU) technologies to eliminate the dependency on rockets to transport materials from Earth and enable scalable construction on Mars.
Our polymer was validated by a third-party lab and proven to outperform concrete in many relevant metrics including tensile and compressive strength, durability under extreme temperatures and higher ductiliy. Being lower atomic mass, it also promises superior cosmic radiation absorption as compared to concrete. It is also an effective thermal resistor.
A vertically oriented cylinder is the best formal basis for a surface habitat. It is the most effective way to reduce loading and maximize usable space since it allows usable space to be aggregated vertically with vertical walls and a compact footprint, keep hoop stress and uplift forces manageable.
This configuration lends itself well to joining and separating mission activities in a meaningful way by level, avoiding the need to divide one large area into many small, confined spaces. In the context of additive manufacturing, vertical cylinders are also inherently the most construct-able shape. Inside, a “double shell” system separates the architectural space from the pressure vessel subject to external conditions, allowing the interior to be high mass-optimized to serve the creation of habitable spaces. The space between the two serves multiple uses including natural daylighting, circulation and maintenance access.
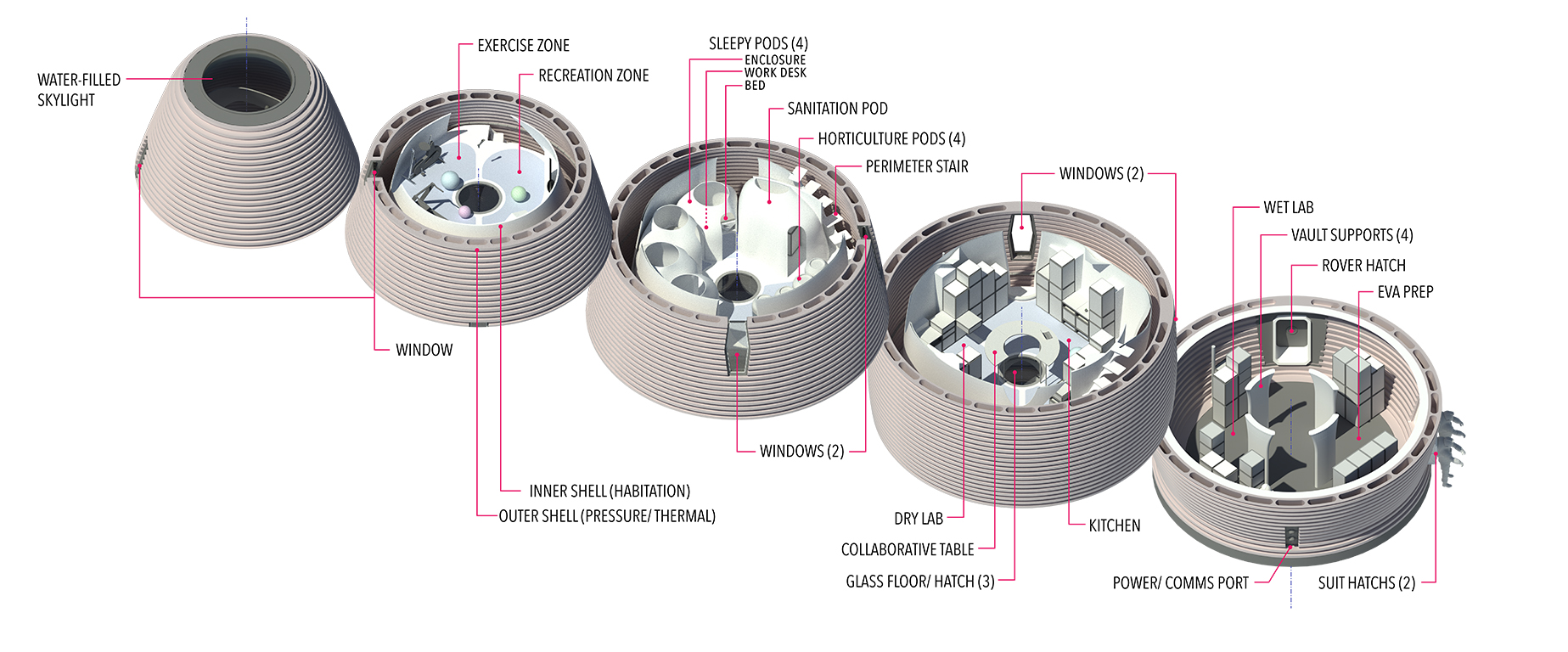
The first towards construction of a prototype was the formulation of a construction material. At our direction Techmer PM formulated a high-performance “Martian polymer”: a basalt fiber-reinforced polylactic acid. This material was novel in that it used a “biopolymer” that can be made from plants high in polysaccarides (sugars) combined with volvanic rock that is known to be relatively abundant on Mars (and the Moon). Eventually, humanity will leverage in-situ resource utilization (ISRU) technologies to eliminate the dependency on rockets to transport materials from Earth and enable scalable construction on Mars.
Our polymer was validated by a third-party lab and proven to outperform concrete in many relevant metrics including tensile and compressive strength, durability under extreme temperatures and higher ductiliy. Being lower atomic mass, it also promises superior cosmic radiation absorption as compared to concrete. It is also an effective thermal resistor.
Once the material was validated, it was only nine weeks until AI SpaceFactory progressed from basic tests to successfully printing, in 24 hrs, a large cylinder designed to hold twelve-hundred gallons of water complete with prefabricated wall penetrations dynamically placed and sealed. At this point, our work had validated by NASA with endorsements totaling $109,000 which were invested in further development.
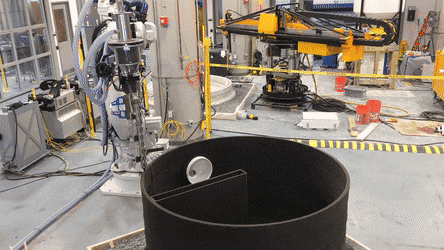
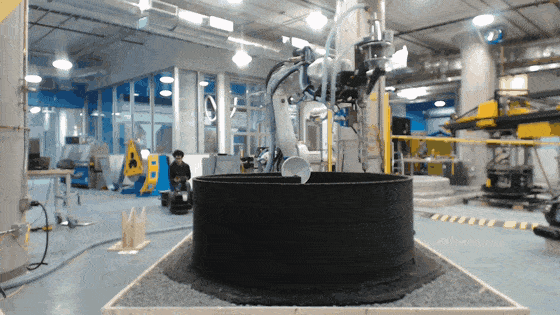
Lessons learned from prototyping and construction were applied to the Design Phase II:
On May 4th, after three phases and $1.6 million awarded, the Challenge came to a dramatic conclusion at Caterpillar’s demonstration facility in Peoria, IL. Forced to print until the last second of allowable time, the team I led at AI SpaceFactory nonetheless won the grand prize of $500,000 by successfully printing a 1:3 scale prototype of the primary structure.
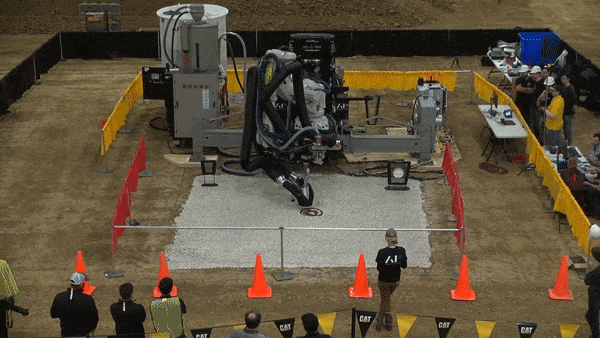
Several documentaries have featured this effort, including Tech Insider, Seeker, and the YouTube Originals series The Age of AI, hosted by Robert Downey Jr.
Project Team
Design Phase 1
Jeffrey Montes (lead)
Sima Shahverdi
David Malott
David Riedel
Michael Bentley
Tony Jin
Construction Phase 1
Jeffrey Montes (Lead)
Christopher James Botham
David Malott
Construction Phase 2
Jeffrey Montes (lead)
Christopher James Botham
David Malott
Design Phase 2
Jeffrey Montes
Construction Phase 3
Jeffrey Montes (lead)
Christopher James Botham
David Riedel
James Earle
James Coleman
Amit Adhikaree
Jeffrey Montes (lead)
Sima Shahverdi
David Malott
David Riedel
Michael Bentley
Tony Jin
Construction Phase 1
Jeffrey Montes (Lead)
Christopher James Botham
David Malott
Construction Phase 2
Jeffrey Montes (lead)
Christopher James Botham
David Malott
Design Phase 2
Jeffrey Montes
Construction Phase 3
Jeffrey Montes (lead)
Christopher James Botham
David Riedel
James Earle
James Coleman
Amit Adhikaree
Consultants & Partners
Design Phases
Structural engineering – Thornton Tomasetti – Dennis C.K. Poon, Chi Chung Tse, Saravanan Panchacharam, Hao Chen
Mechanical/ structural testing – Simpson, Gumpertz & Heger
Lighting design – Arup – Haniyeh Mirdamadi
Concrete engineering consultant – Dr. Victor Li (University of Michigan)
Polymer design – Techmer PM – Alan Franc, Tom Drye
Mars geochemistry consultant– Dr. Scott McLennan (Stony Brook University)
Planetary physics consultant – Dr. Philip Metzger (University of Central Florida)
Systems and civil engineering consultant– Dr. Paul van Susante (Michigan Tech)
ISRU consultant – Dr. Kris Zacny (Honeybee Robotics)
Basalt construction consultant– Rodrigo Romo, Kyla Edison (PISCES)
Building energy performance consultant- Duncan Phillips (RWDI)
Structural engineering – Thornton Tomasetti – Dennis C.K. Poon, Chi Chung Tse, Saravanan Panchacharam, Hao Chen
Mechanical/ structural testing – Simpson, Gumpertz & Heger
Lighting design – Arup – Haniyeh Mirdamadi
Concrete engineering consultant – Dr. Victor Li (University of Michigan)
Polymer design – Techmer PM – Alan Franc, Tom Drye
Mars geochemistry consultant– Dr. Scott McLennan (Stony Brook University)
Planetary physics consultant – Dr. Philip Metzger (University of Central Florida)
Systems and civil engineering consultant– Dr. Paul van Susante (Michigan Tech)
ISRU consultant – Dr. Kris Zacny (Honeybee Robotics)
Basalt construction consultant– Rodrigo Romo, Kyla Edison (PISCES)
Building energy performance consultant- Duncan Phillips (RWDI)
Construction Phases
Autodesk Technology Center Boston
Virginia Tech Center for Design Research
Macromolecules Innovation Institite at Virginia Tech
Virginia Tech Center for Design Research
Macromolecules Innovation Institite at Virginia Tech
Acknowledgements
The construction effort was a major endeavor
requiring the support and expertise of outside persons and institutions.
The team is grateful to Techmer PM for taking a business risk, formulating the Marsha-α polymer and delivering it in a timely manner.
It is hard to properly acknowledge the game-changing support from Autodesk Technology Center Boston. Without their training, expert advice and zen-like patience, this project would not have been possible and members of the Marsha-α team would be working on less interesting projects today. Thank you to Adam Allard, Joe Aronis, Stefanie Pender, Taylor Tobin, Athena Moore, Adam Day, Zack Tenaglia, Josh Aigen and Hannah Rossi.
Virginia Tech Center for Design Innovation supported the effort with an equipment loan and by lending their hands-on help in Peoria during the final print. Thank you to Nathan King, Bob Dunay, Joseph Kubalak, Benjamin Woods, Kaelum Hasler, and Callan McGill.
Caterpillar Edwards Demonstration and Learning Facility, where the final event happened, showed great professionalism and made every effort to accommodate last-minute needs while maintaining a safe environment.
Finally, thanks to NASA Centennial Challenges and for their vision in creating this Challenge. It has altered the course of Space technology and changed the course of the team’s careers for the better.
The team is grateful to Techmer PM for taking a business risk, formulating the Marsha-α polymer and delivering it in a timely manner.
It is hard to properly acknowledge the game-changing support from Autodesk Technology Center Boston. Without their training, expert advice and zen-like patience, this project would not have been possible and members of the Marsha-α team would be working on less interesting projects today. Thank you to Adam Allard, Joe Aronis, Stefanie Pender, Taylor Tobin, Athena Moore, Adam Day, Zack Tenaglia, Josh Aigen and Hannah Rossi.
Virginia Tech Center for Design Innovation supported the effort with an equipment loan and by lending their hands-on help in Peoria during the final print. Thank you to Nathan King, Bob Dunay, Joseph Kubalak, Benjamin Woods, Kaelum Hasler, and Callan McGill.
Caterpillar Edwards Demonstration and Learning Facility, where the final event happened, showed great professionalism and made every effort to accommodate last-minute needs while maintaining a safe environment.
Finally, thanks to NASA Centennial Challenges and for their vision in creating this Challenge. It has altered the course of Space technology and changed the course of the team’s careers for the better.
Honeybee Robotics
client: Honeybee Robotics
my role/scope: concept development, modelling and visualization
type: contract
iSEE
In-situ Spectroscopic Europa Explorer
iSEE is a next-generation ultra-compact Raman system with superior performance that meets the top-level scientific requirements of multiple planetary missions to the inner and outer Solar System.
from Programmable Raman Sensing For In-situ Planetary Exploration, P. Sobron, L. Barge, A. Davila, M. Fahey, M. Krainak, F. Rehnmark, A. Yu, K. Zacny.
![]()
from Programmable Raman Sensing For In-situ Planetary Exploration, P. Sobron, L. Barge, A. Davila, M. Fahey, M. Krainak, F. Rehnmark, A. Yu, K. Zacny.
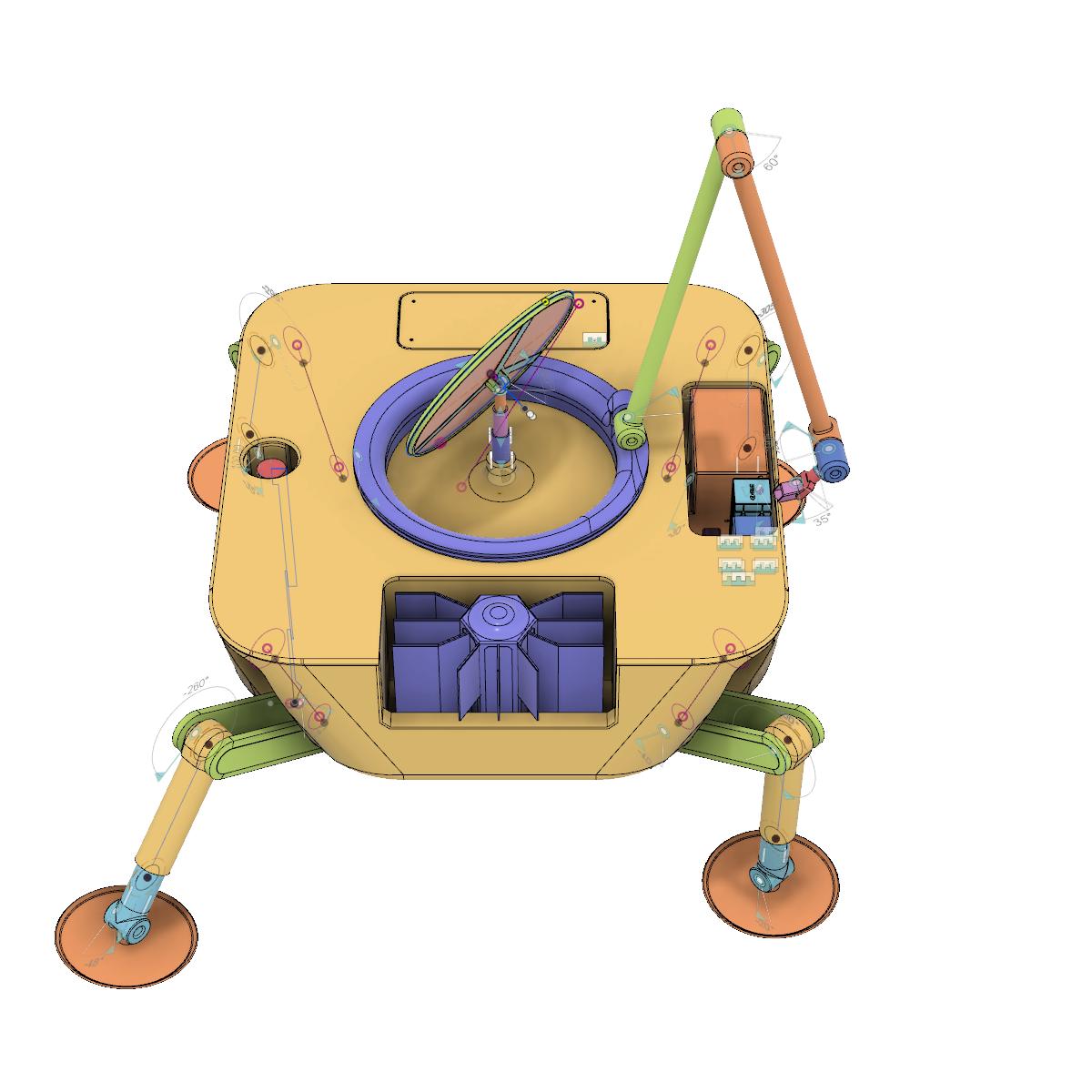

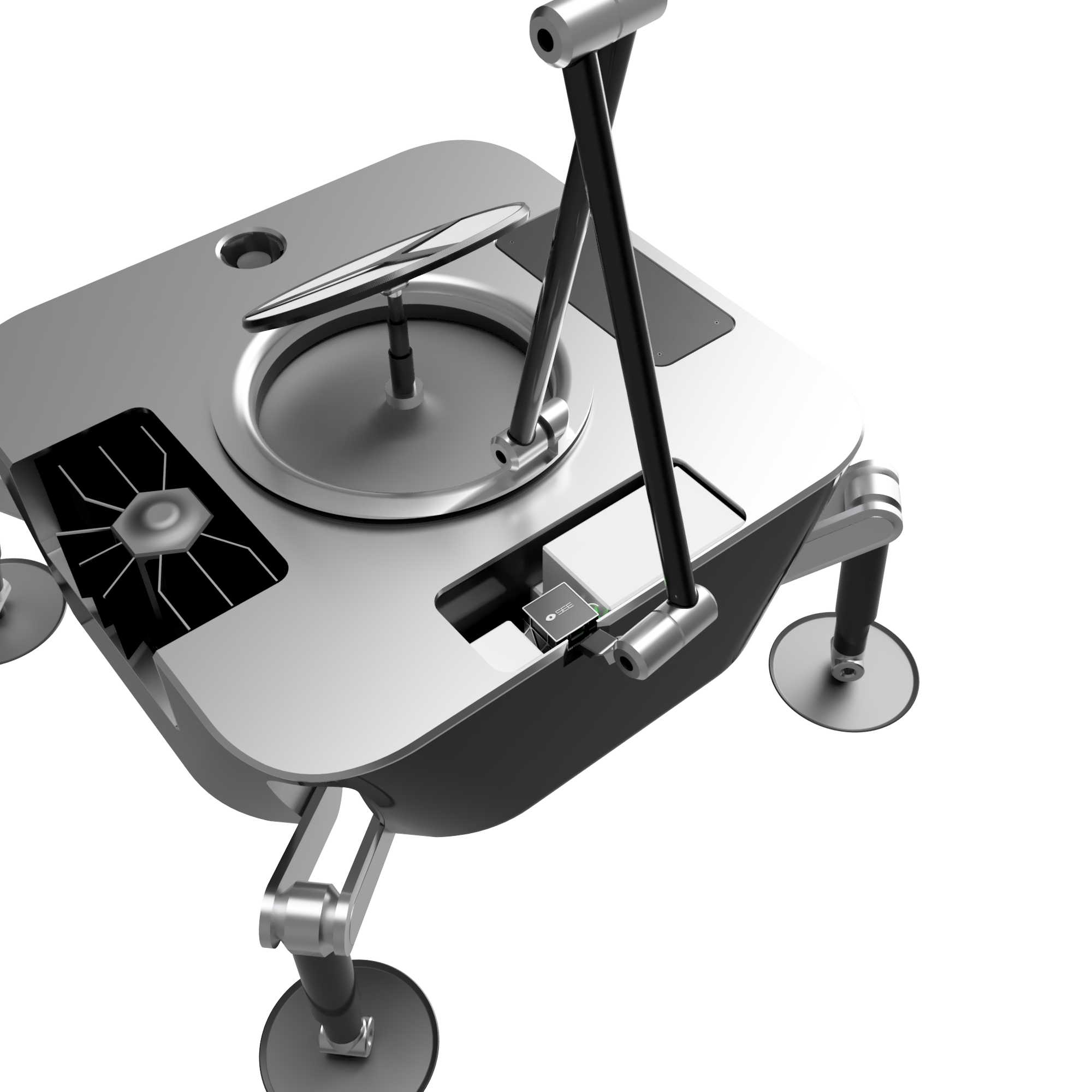
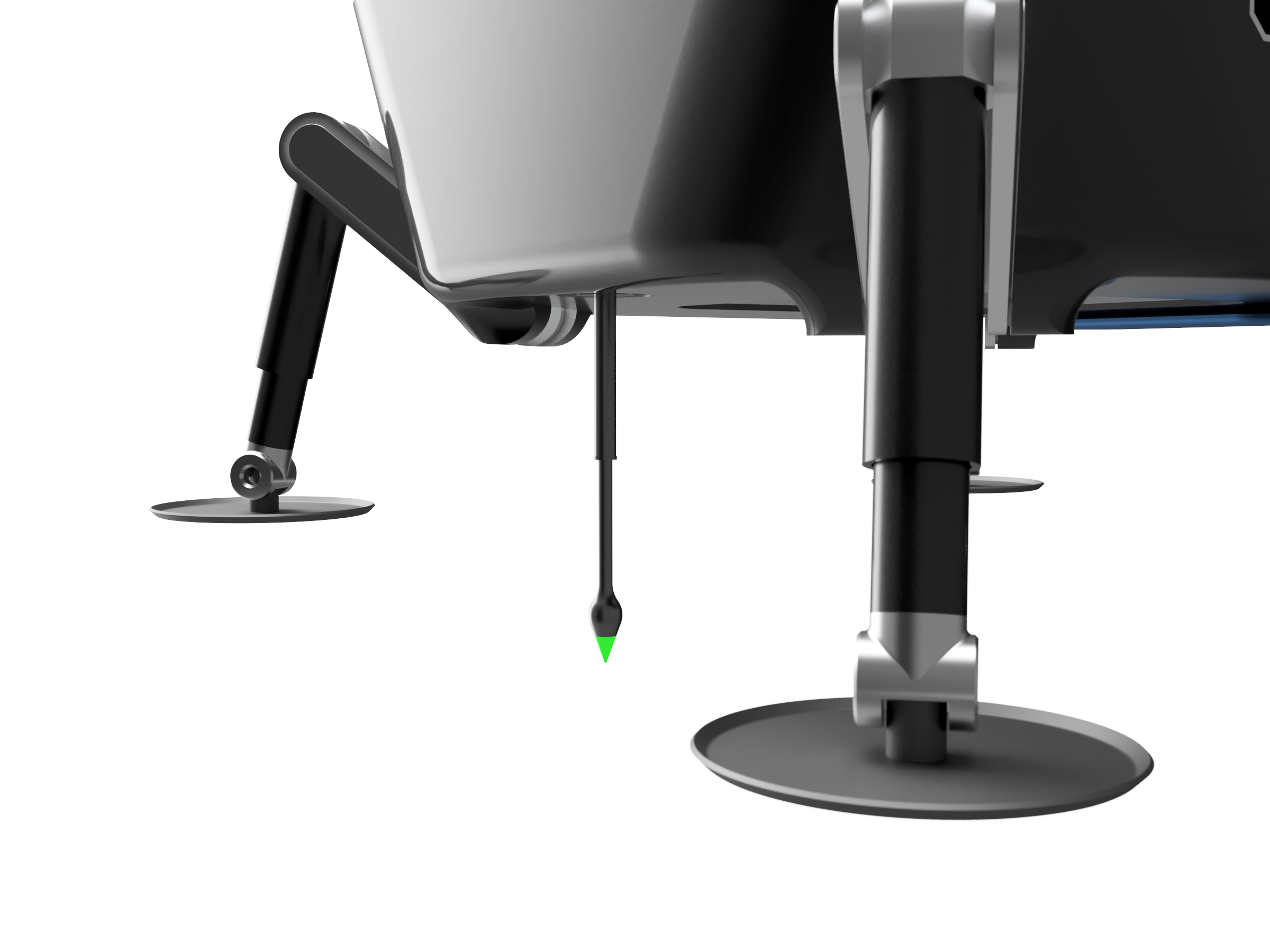
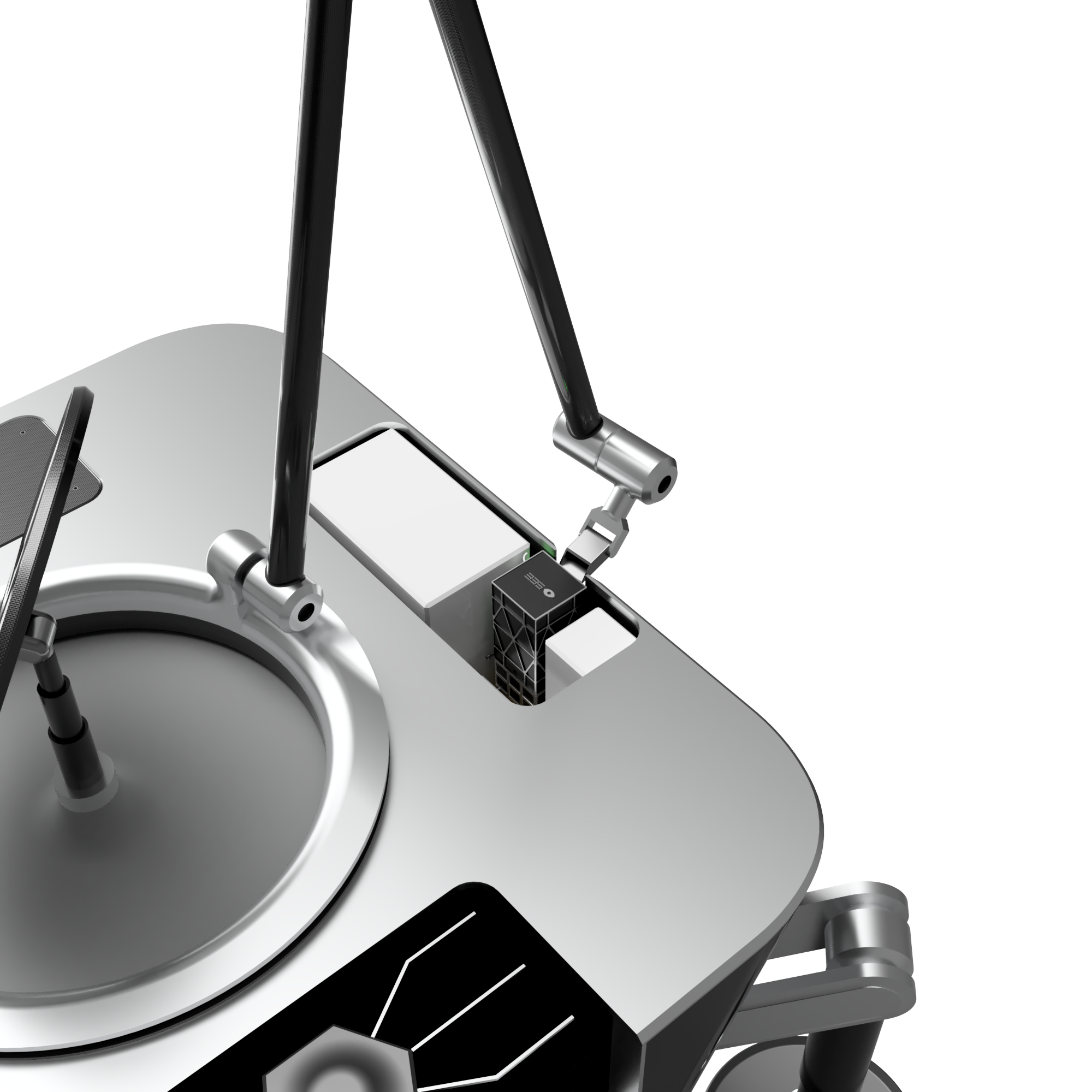
MOONShot
Moon Subsurface Hydrogen Optical Tool
“MoonSHOT is a next-generation ultra-compact laser spectroscopy system equipped with a fiber optic sensing probe that enables in-situ geochemical and mineralogical analysis and mapping of Moon surface and shallow-subsurface samples in a remote location without having to extract a sample and bring it to a spectrometer.
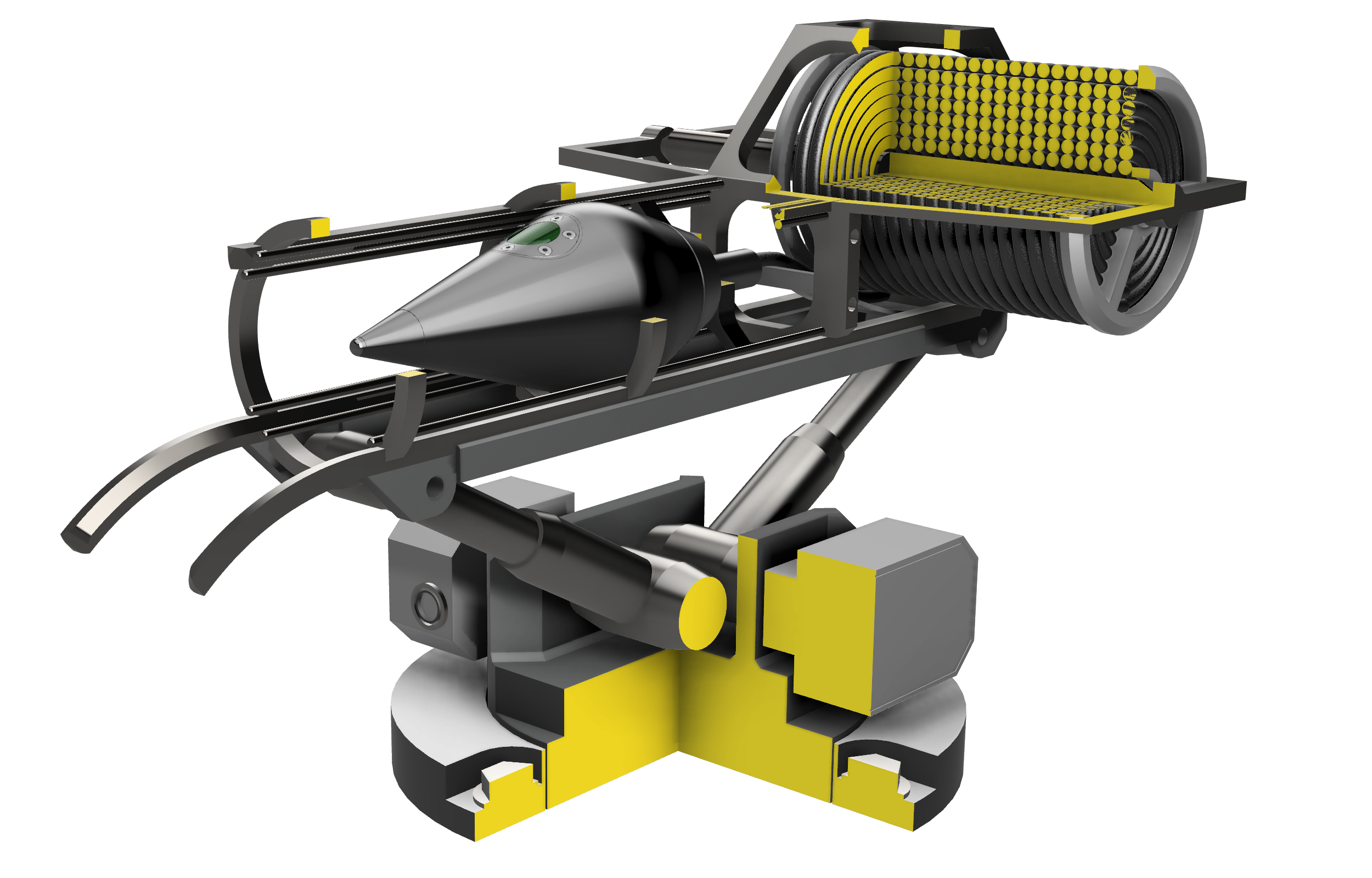
Fig 1. Penetrator launcher
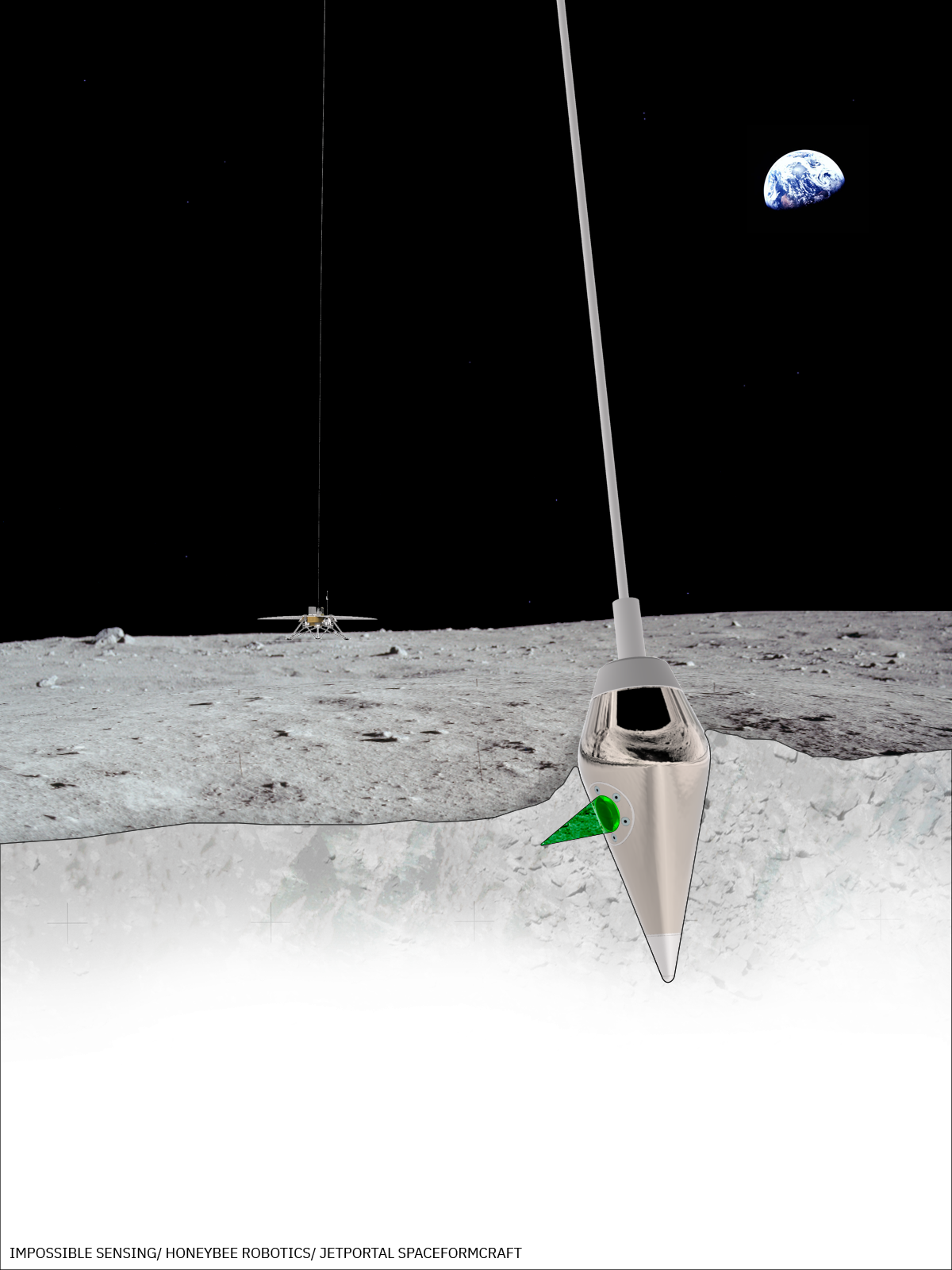
Fig. 2: Long distance surface penetration and sensing
text from: Redeployable sensor probe for in-situ lunar resource mapping from small landers, P. Sobron, M. Fahey, M. Krainak, A. Misra, F. Rehnmark, A. Wang, A. Yu, K. Zacny, R. Zeigler.
RedWater
Extraction of Water from Mars’ Ice Deposits
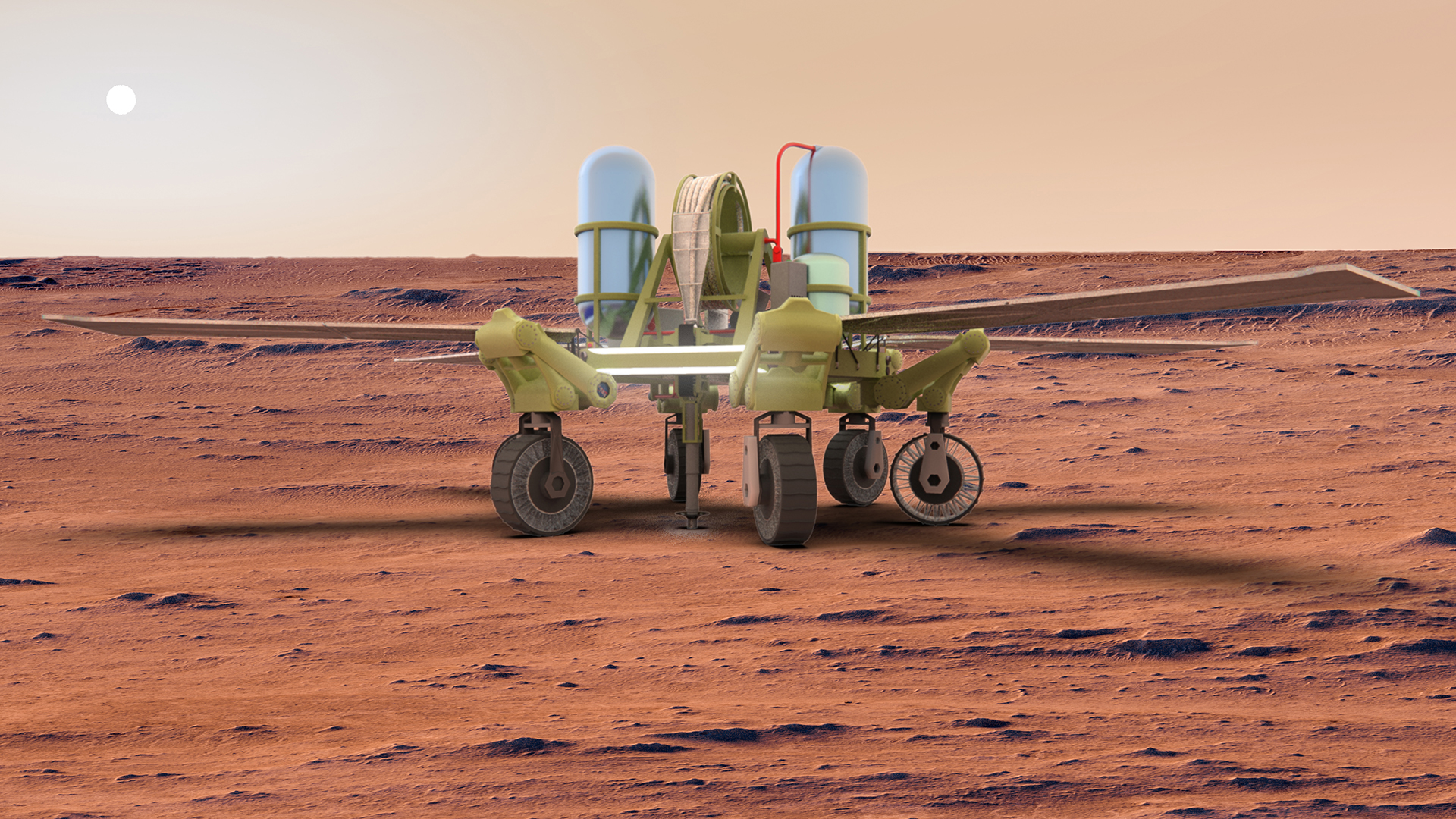
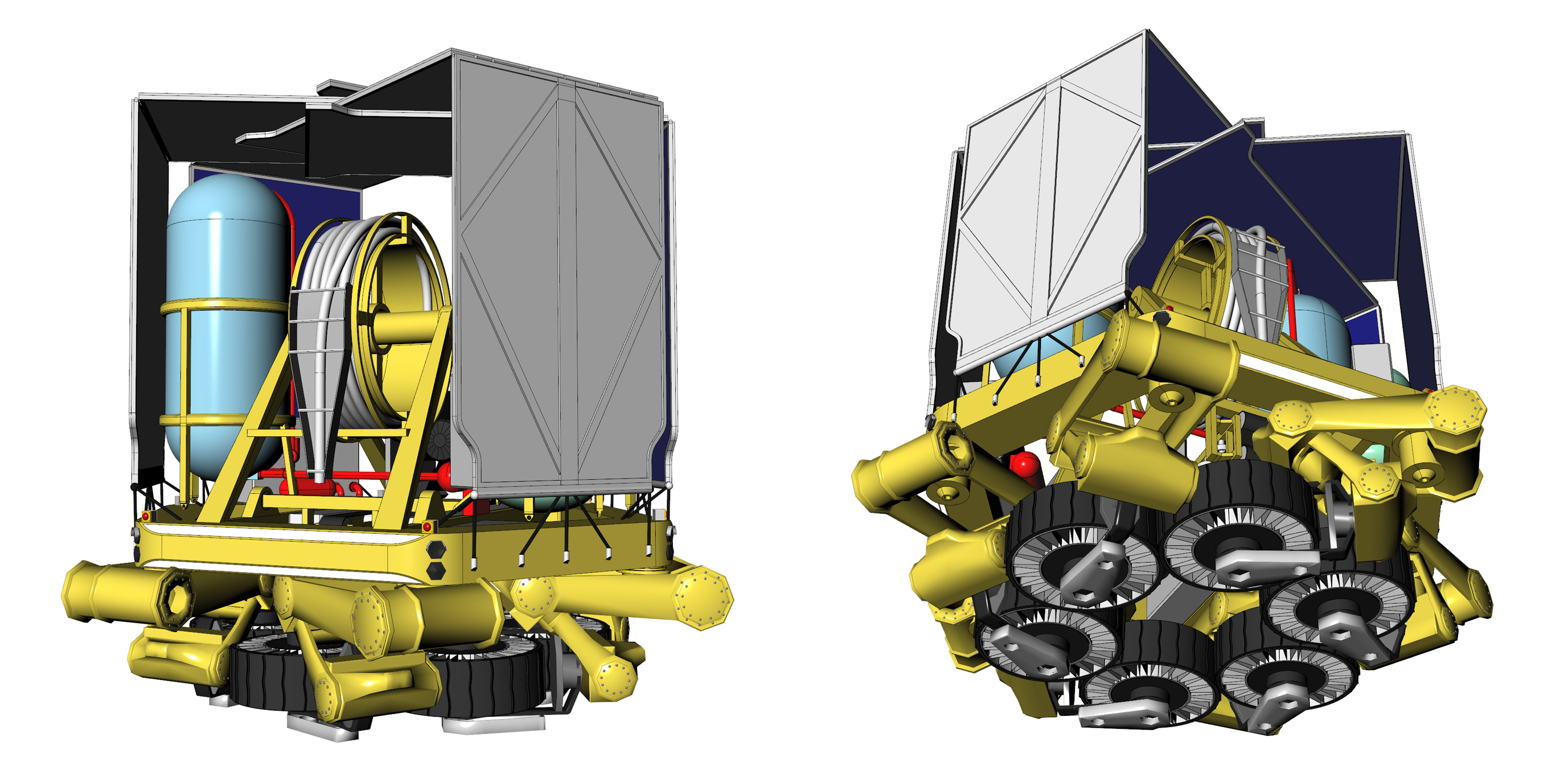
“The RedWater system combines the two technologies into one. It uses the Coiled Tubing approach to create a drill hole. Once the hole is made, the coiled tubing is left in the hole and used as conduit for water extraction. The Bottom Hole Assembly contains a rotary-percussive drill subsystem, a downhole pump, and heaters. The tube houses an insu-lated and heated hose as well as wires for downhole motors and heaters. During drilling, compressed gas is sent downhole through the hose. The gas escapes through the annular space between the tube and borehole wall and removes cuttings that can be collected and analyzed for science. Upon reaching an ice layer, the drill continues for another ~3 m and then stops advancing forward, but the bit continues to spin. Heaters are turned on to melt the surrounding ice. Once ice starts to melt, the peristaltic pump starts pumping a fraction of the melted water up the same hose that was used for the compressed gas, and into a storage tank on the surface via a three-way heated valve, which switches between the gas tank and the water tank. The remaining water passes through a downhole heater and is pumped into the rotating bit for water jetting. This continuous stirring and the injection of hot water speeds up the melting process. After melting a section of ice, the CT is reactivated to drill further into the underlying ice and the melting process continues.
“Since atmospheric pressures and temperatures in the Martian northern plains extends above water’s triple point, liquid water can exist at the surface. However, it is unstable and will boil off very quickly. For this reason, it is desirable to seal off the hole. This can be achieved via active means (e.g., a packer can expand in the hole and seal off the annular space between the tube and the borehole) or passive means (e.g., water vapor would recondense on the cold borehole wall and seal it; this in fact has been observed). In the latter case, the tube would have to be heated to free itself up before continuing further down, when needed.
Text by technical proposal team
Proposal Team
K. Zacny, Honeybee Robotics
M. Hecht, Haystack Observatory, Massachusetts Institute of Technology
N. E. Putzig, Planetary Science Institute
D. Sabahi, NASA JPL -retired
P. van Susante, Michigan Technological University
M. Hecht, Haystack Observatory, Massachusetts Institute of Technology
N. E. Putzig, Planetary Science Institute
D. Sabahi, NASA JPL -retired
P. van Susante, Michigan Technological University
The Snail
Martian Mobile Water Production
The overall objective of “The Snail” is to demonstrate an innovative process for extraction of water from hard extraterrestrial soils. The process involves ‘dissolving’ and disaggregating the hard surface material under a dome using water jet to form a slurry then pumping the slurry into the water extraction system.
The overall objective of “The Snail” is to demonstrate an innovative process for extraction of water from hard extraterrestrial soils. The process involves ‘dissolving’ and disaggregating the hard surface material under a dome using water jet to form a slurry then pumping the slurry into the water extraction system.
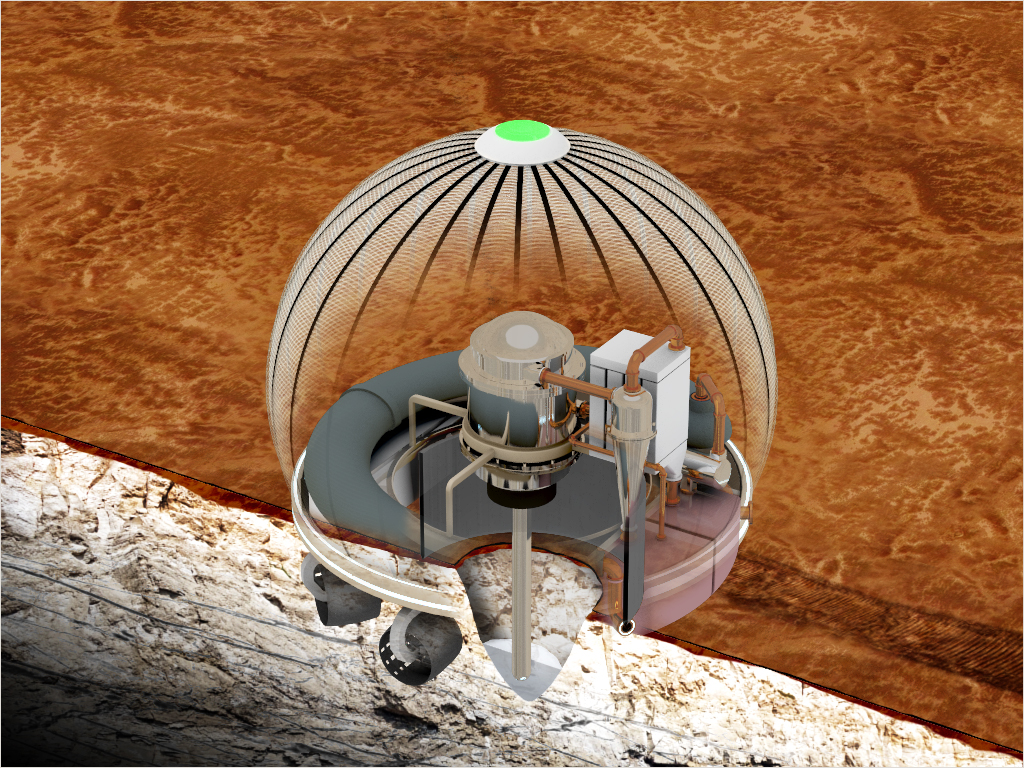
Proposal Team
PI: Jeffrey Allen (MTU)
Co-I: Timothy Eisele (MTU)
Co-I: Ezequiel Medici (MTU)
Co-I: Paul van Susante (MTU)
Co-I: Kris Zacny (Honeybee Robotics)
Co-I: Timothy Eisele (MTU)
Co-I: Ezequiel Medici (MTU)
Co-I: Paul van Susante (MTU)
Co-I: Kris Zacny (Honeybee Robotics)
NASA Mars Ice Home
Martian Ice Shelter Conceptclient: NASA
my role/scope: architectural design (in collaboration with SEArch and Clouds AO)
type: contract
In early 2016, researchers at NASA's Langley Research Center reached out to the design team responsible for Mars Ice House (2015) to collaborate on a new project for a translucent Martian surface habitat made of water ice - a safer and more livable alternative to “aluminum can” concepts usually considered for Mars architectures.
The project, named Mars Ice Home (Home being a conjunction of house and dome), is an ongoing collaboration between NASA engineers and architects that combines the rigor of first-principle design with a focus on human habitability, programmatic occupation and cultural and aesthetic impact.
The first design of the habitatm, completed in 2016, centered on a toroidal pressure structure covered in a mass of Martian water ice segmented into quadilateral cells, which could be filled in parallel or in sequence. The ice shell was penetrated with three equispaced hatches which could accomodate crew (two) and cargo (one).
The project, named Mars Ice Home (Home being a conjunction of house and dome), is an ongoing collaboration between NASA engineers and architects that combines the rigor of first-principle design with a focus on human habitability, programmatic occupation and cultural and aesthetic impact.
The first design of the habitatm, completed in 2016, centered on a toroidal pressure structure covered in a mass of Martian water ice segmented into quadilateral cells, which could be filled in parallel or in sequence. The ice shell was penetrated with three equispaced hatches which could accomodate crew (two) and cargo (one).
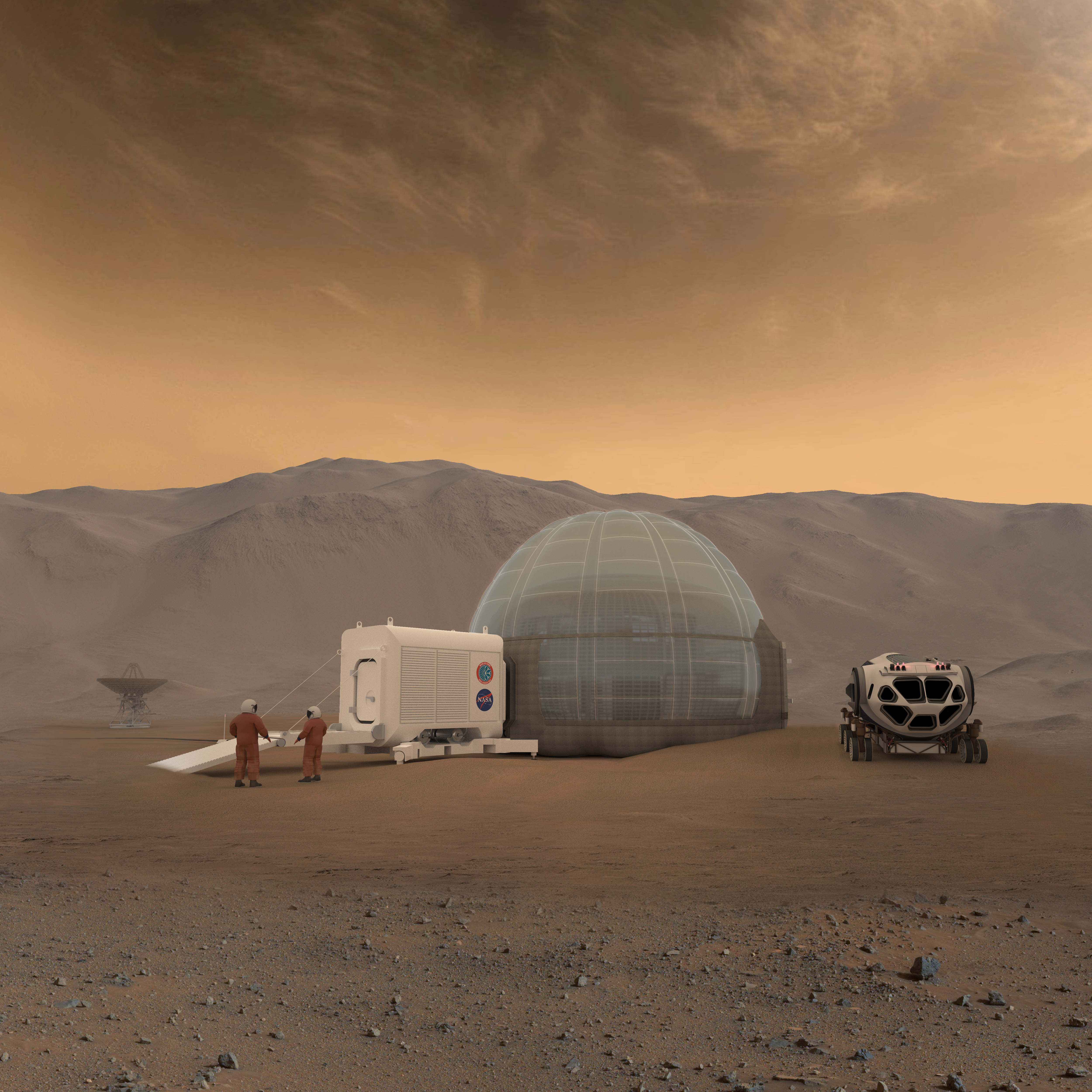
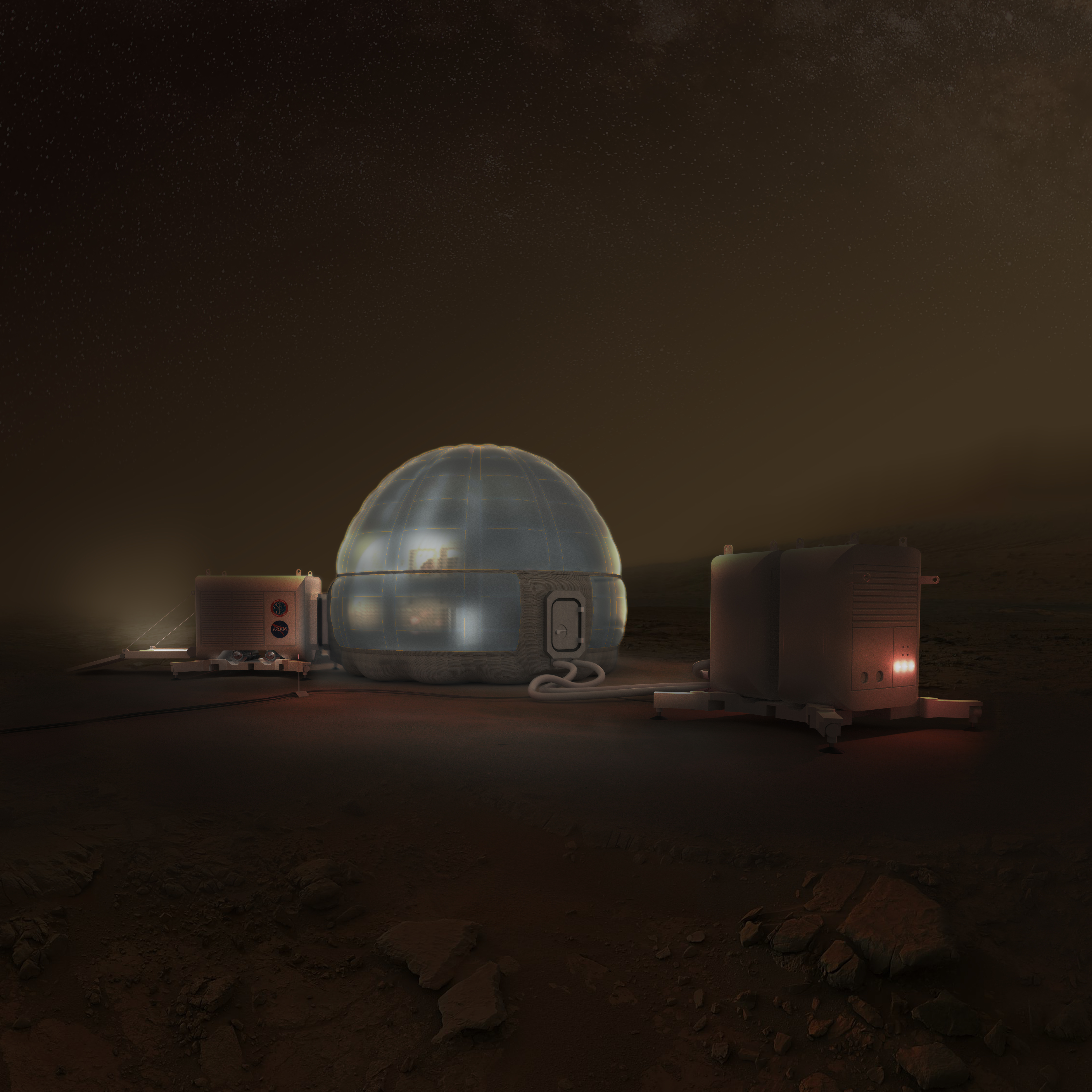
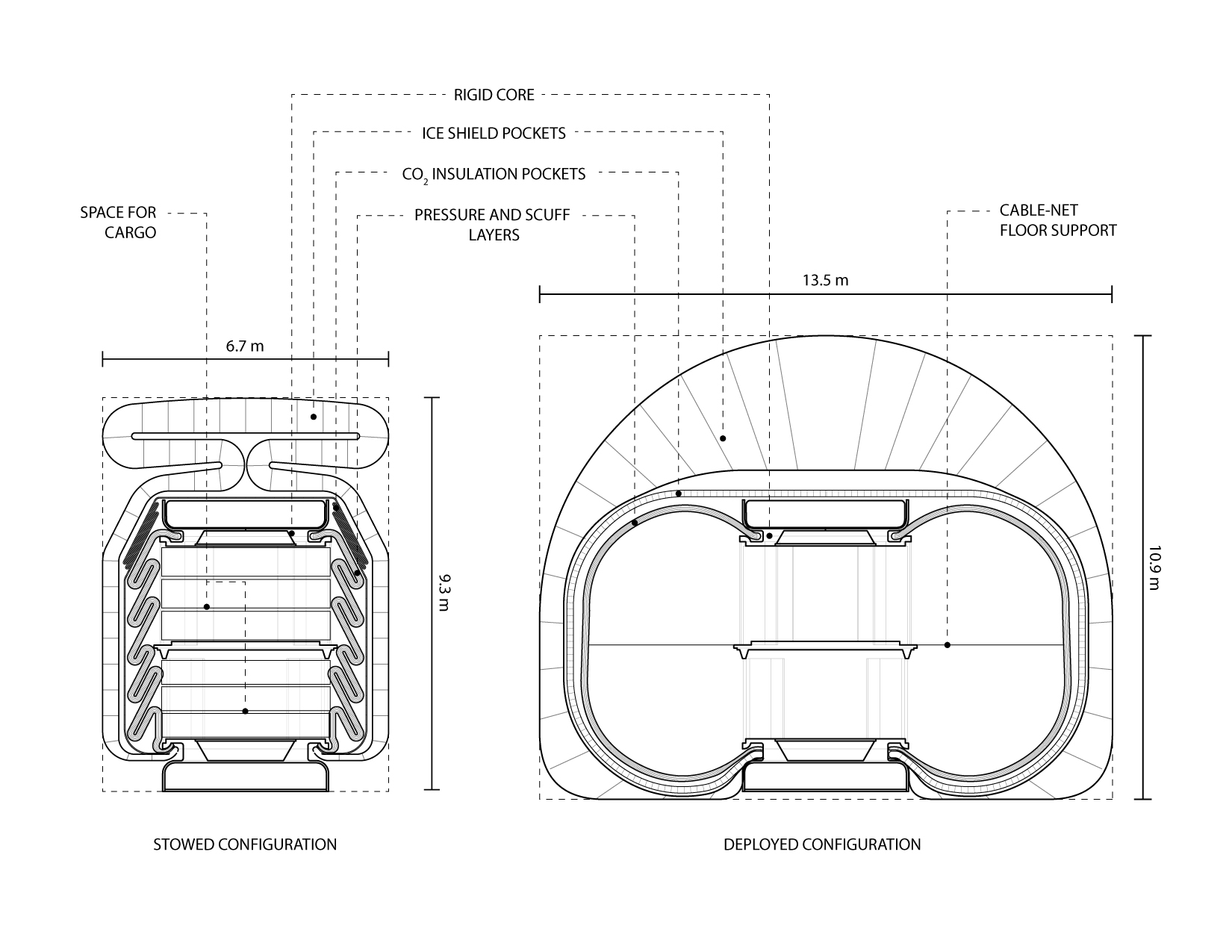
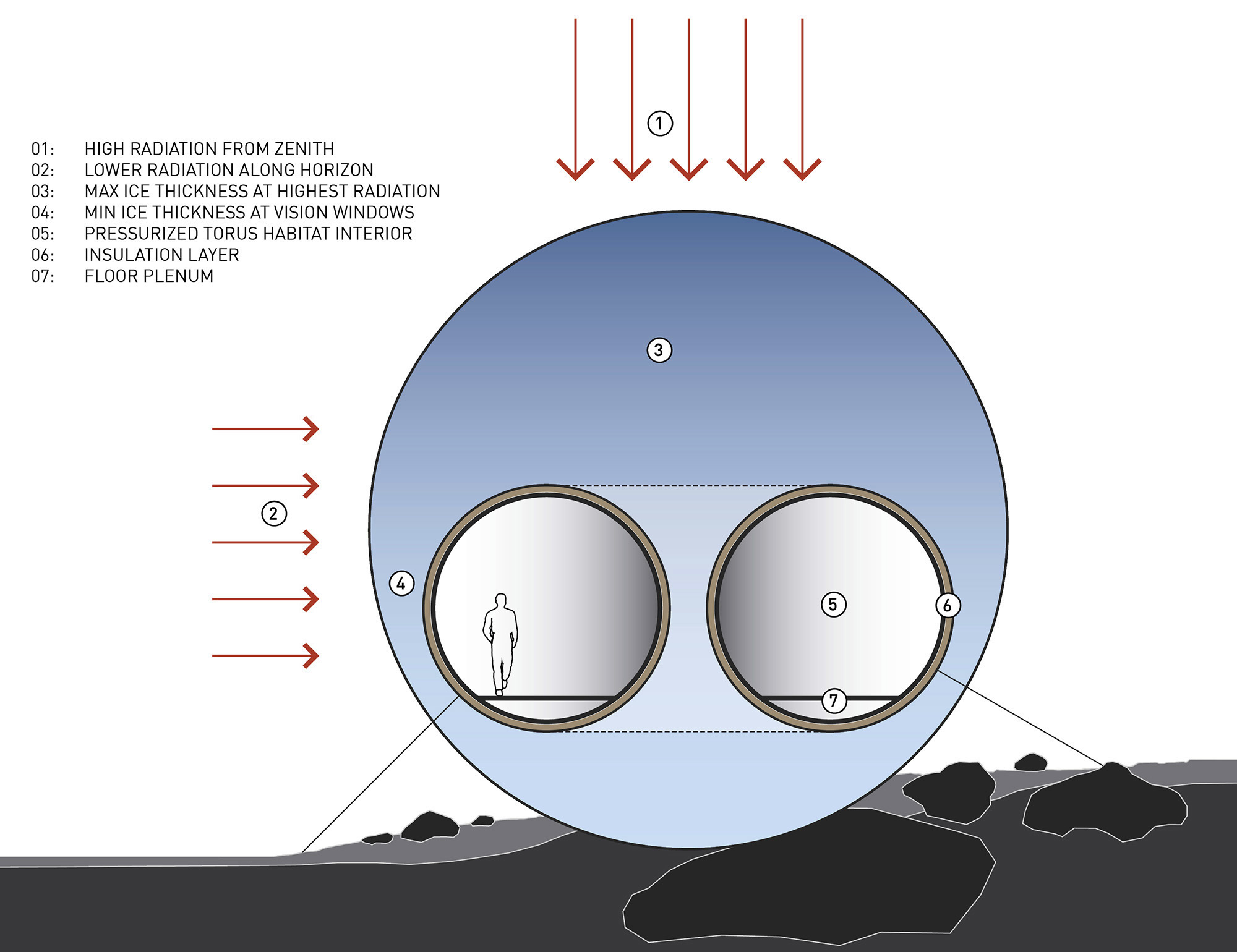
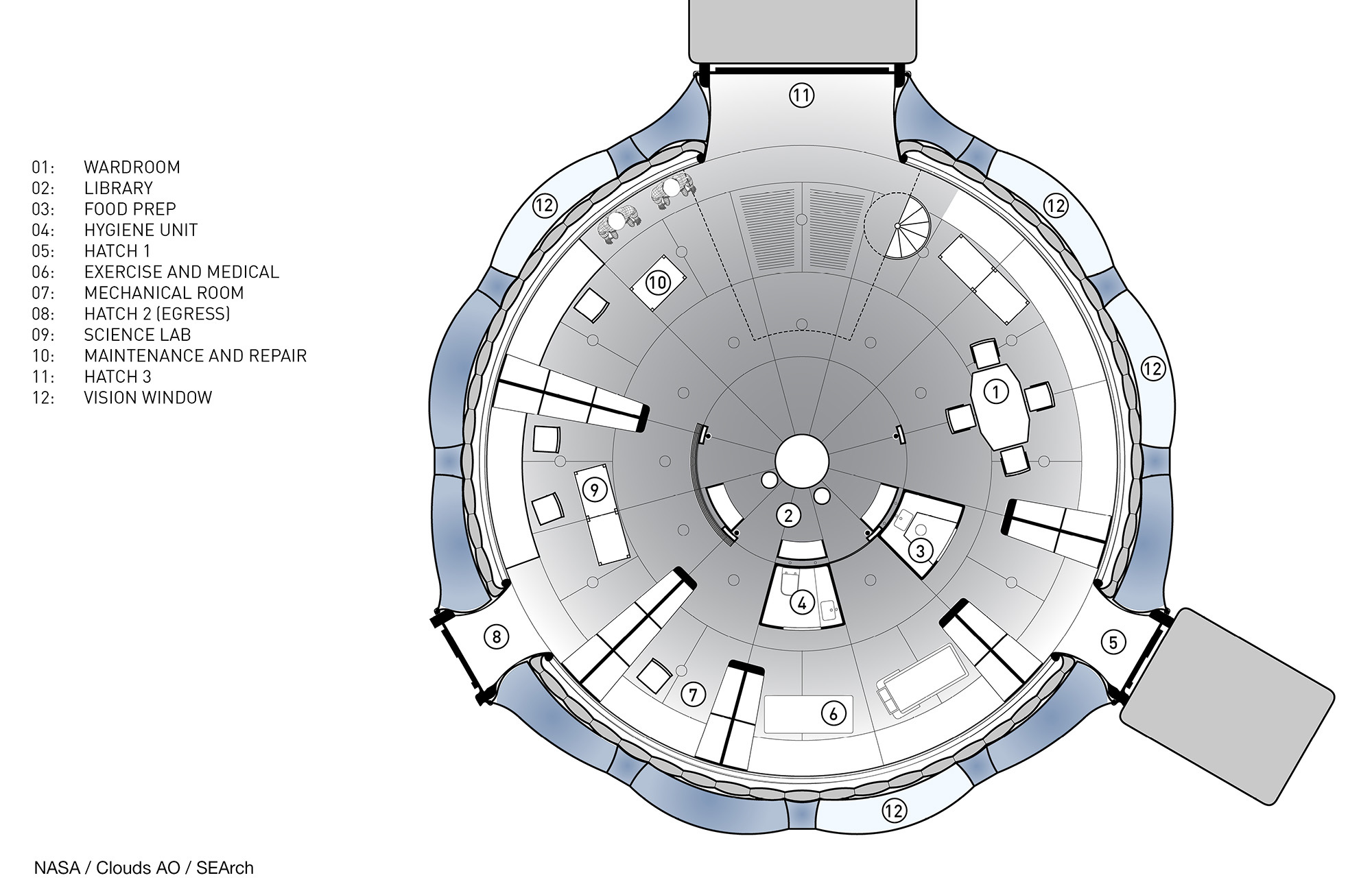
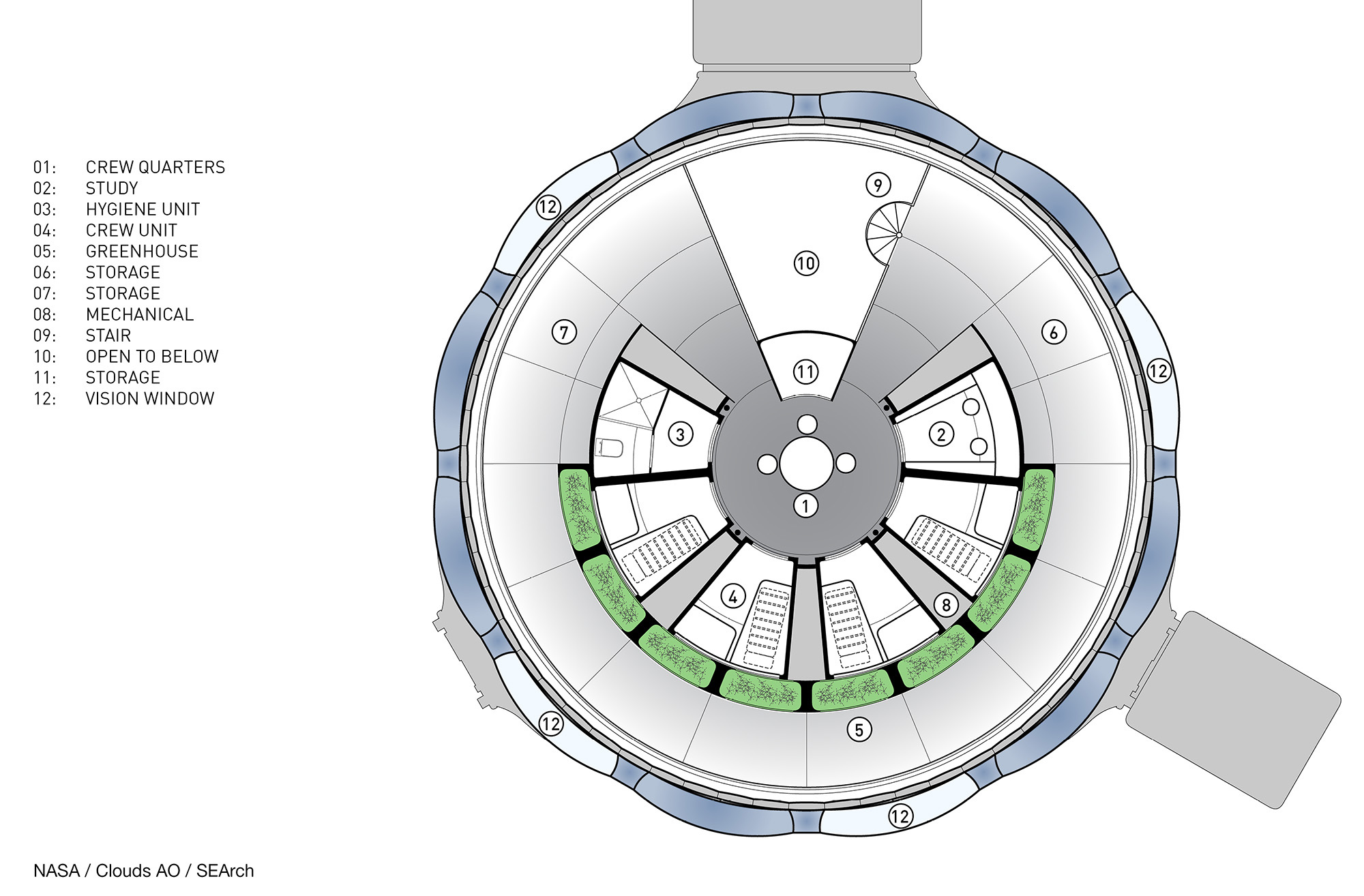
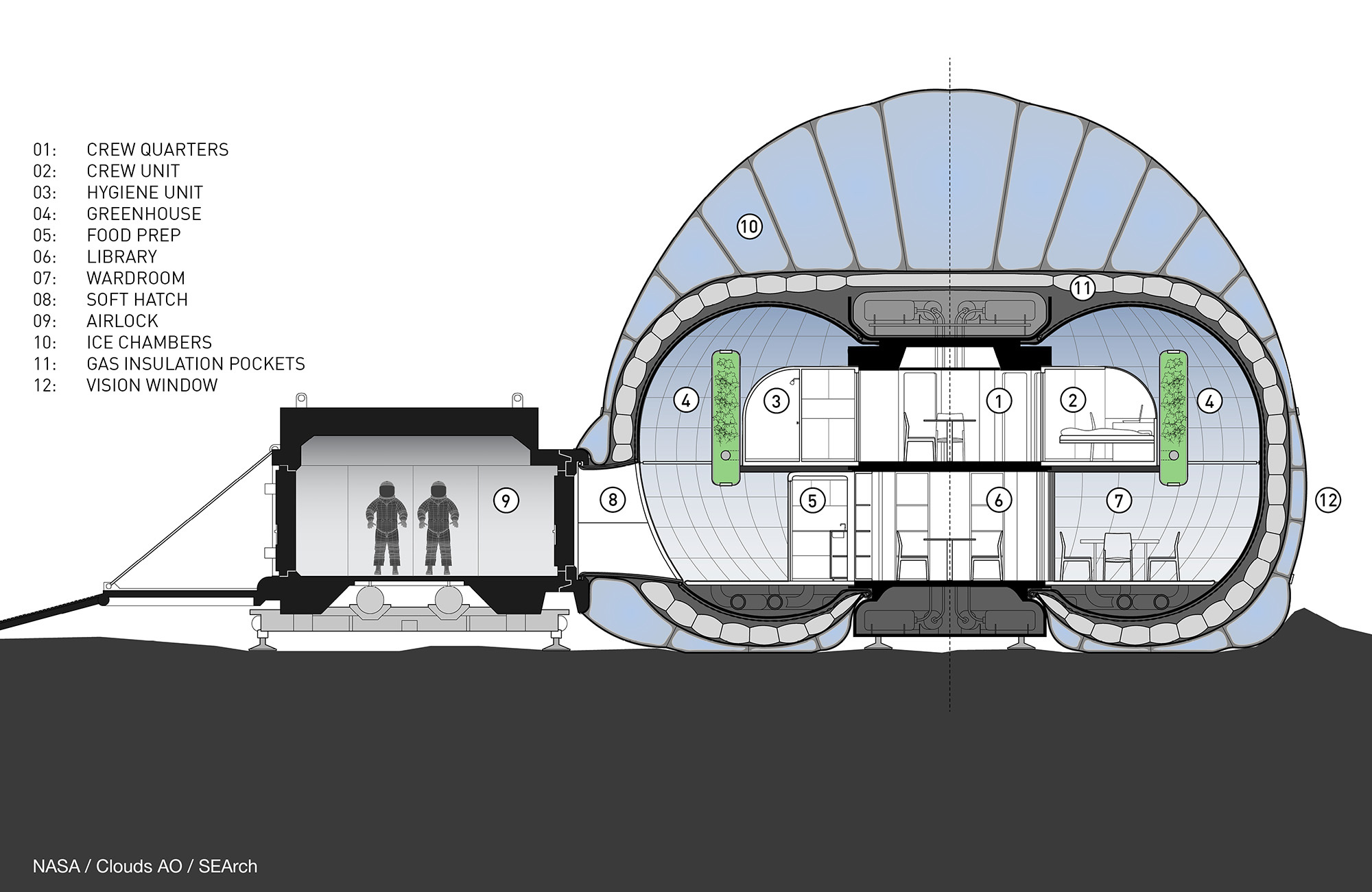
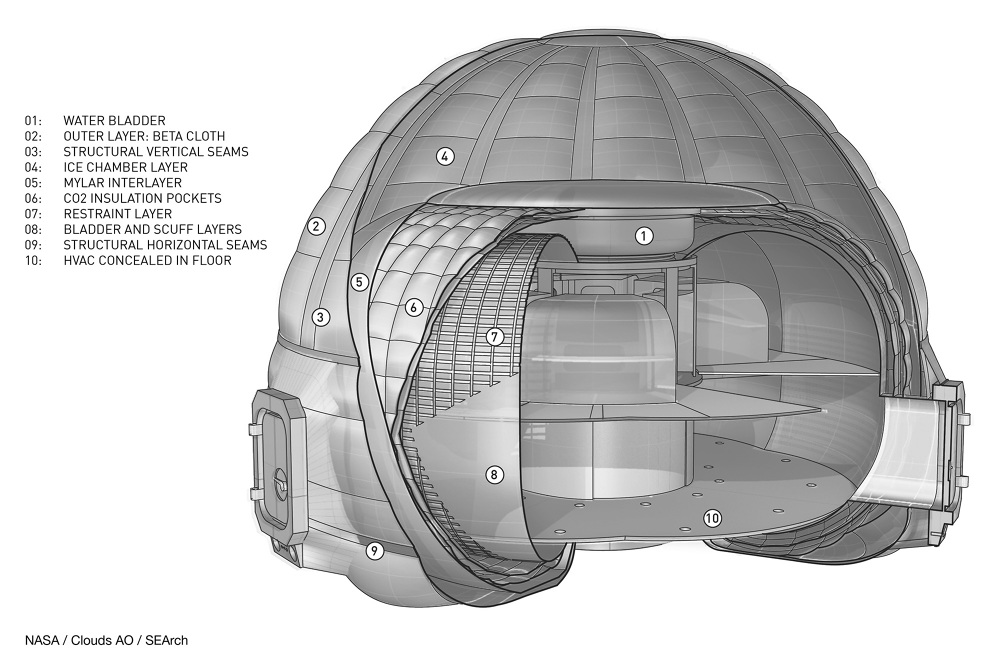
The second version, completed in 2017, took a closer look at the mechanics of ice, the sequence of filling and freezing, the ice cell configuration and its potential fabrication. This resulted in a vertical configuration for the ice cells that could be filled as air beam windows between columns provided support during the filled process. The completed structure now features integrated windows, and does not rely on the ice and the membranes containing it to be transparent.
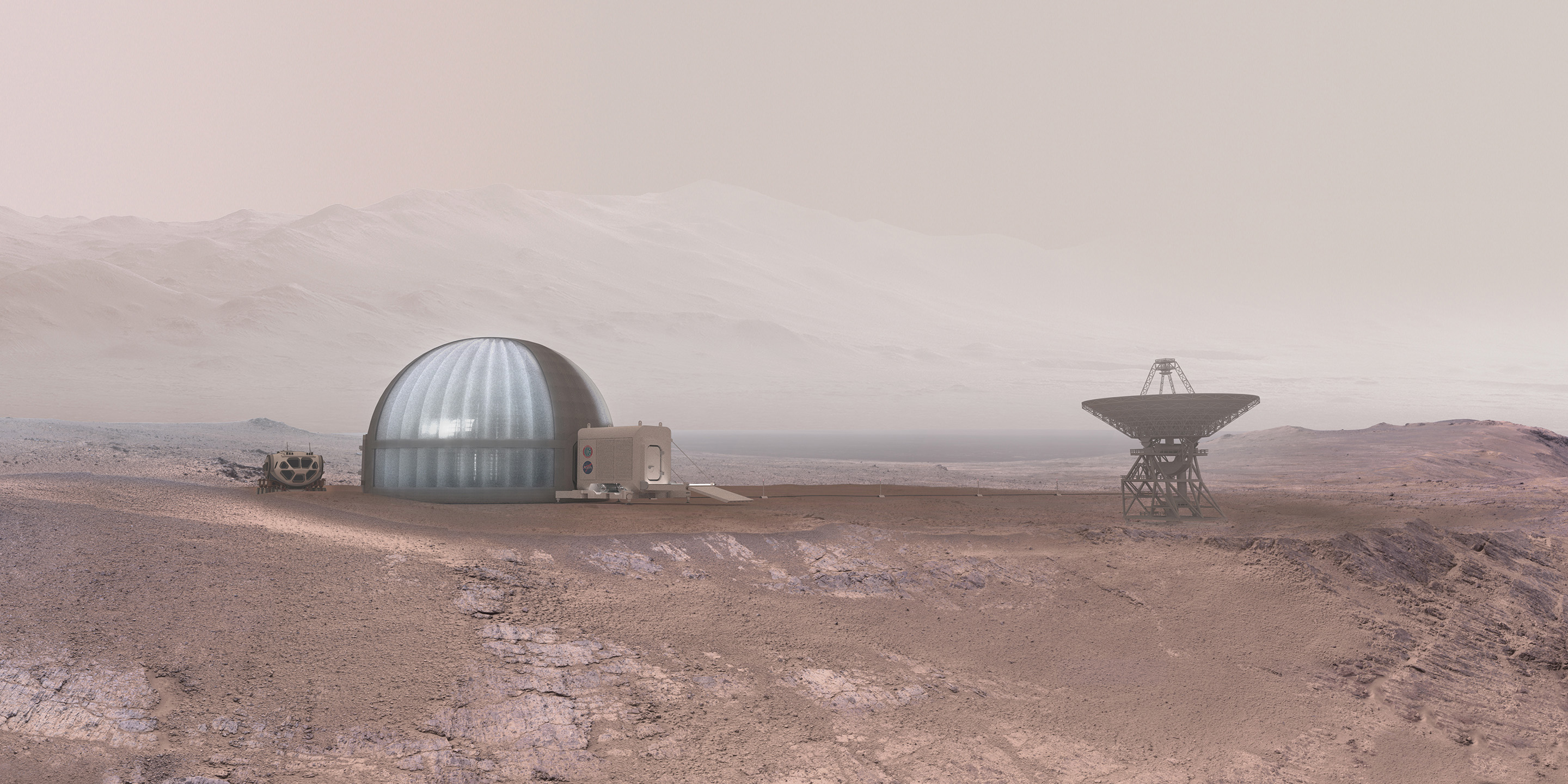
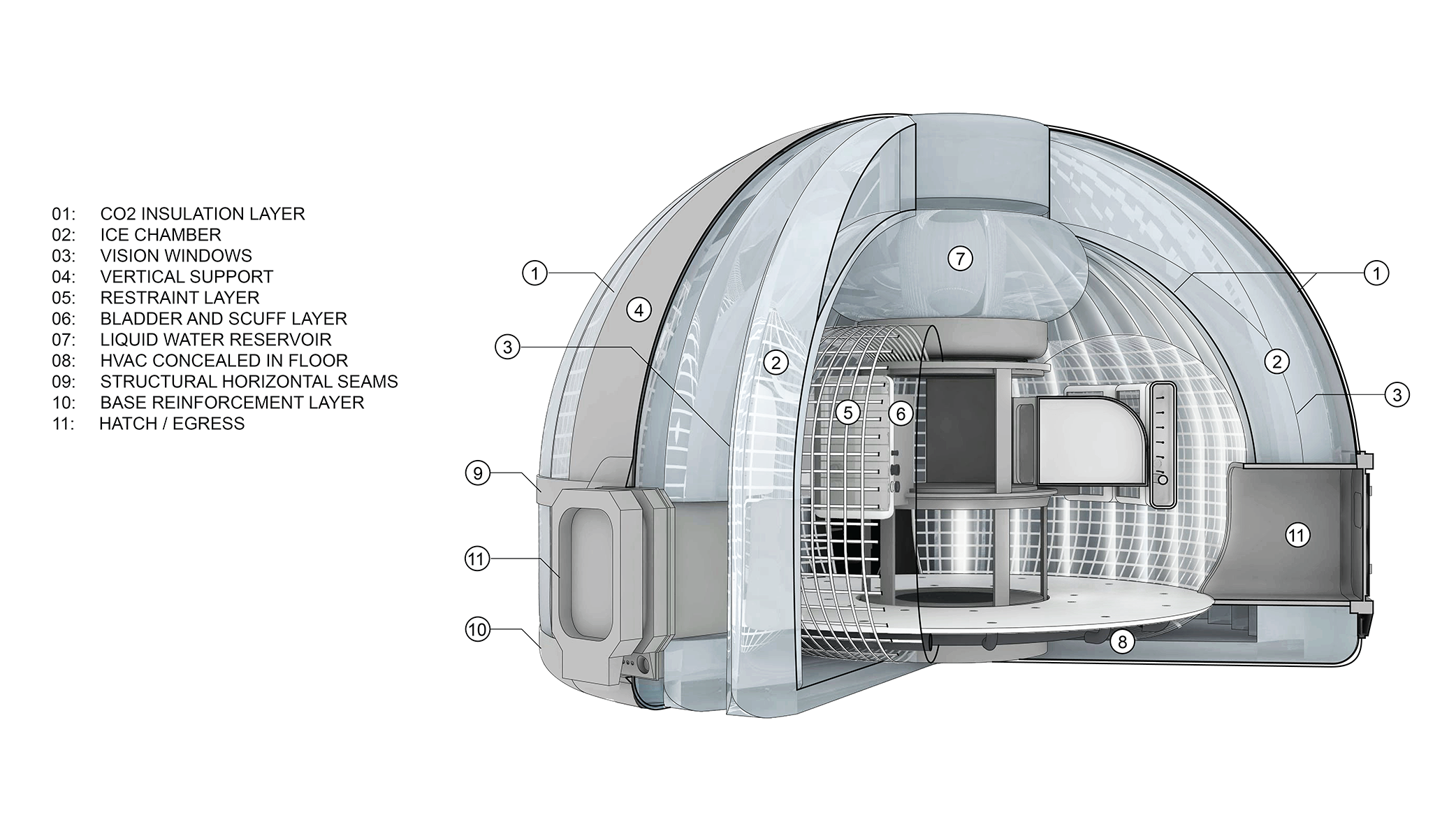
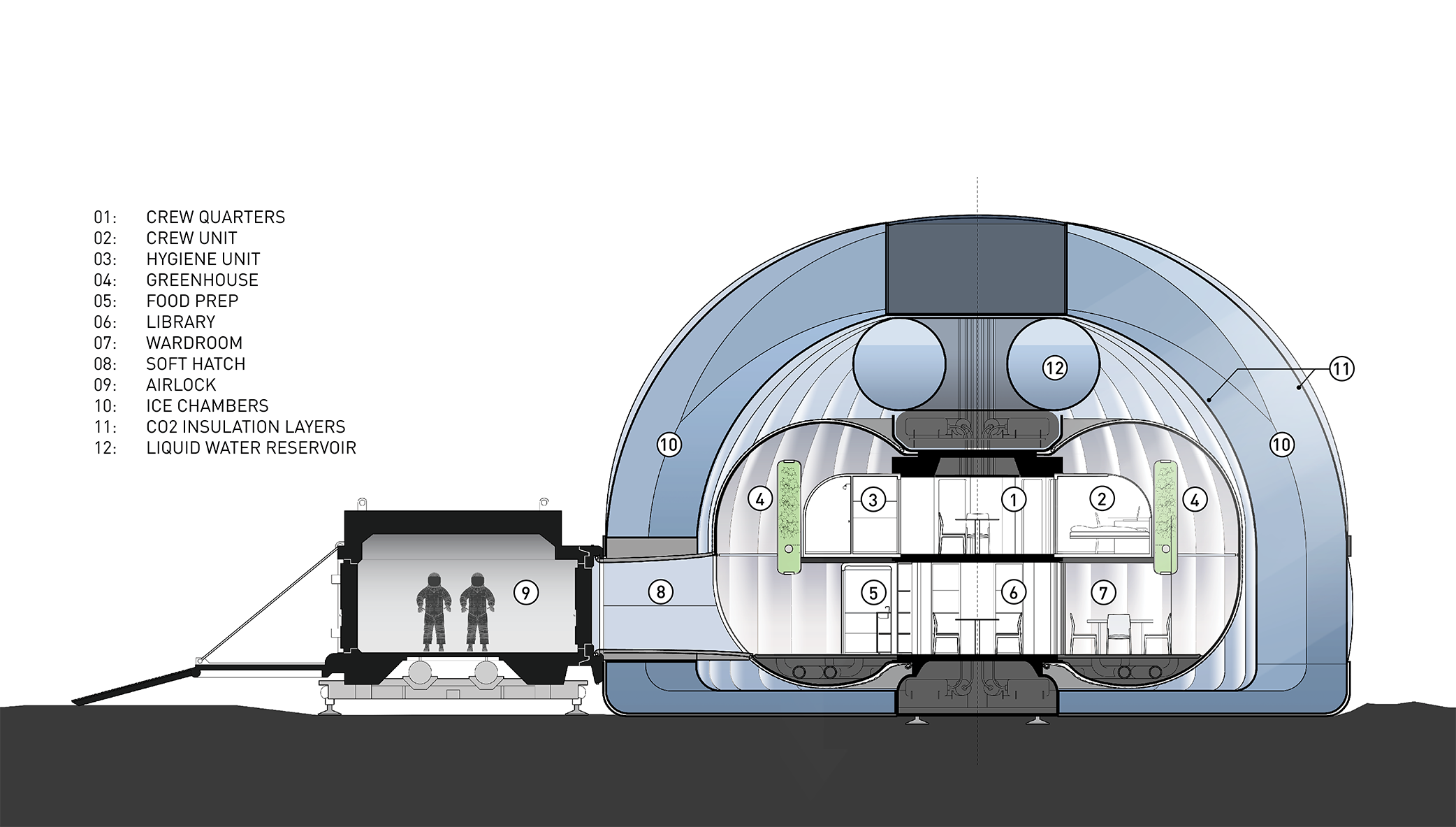
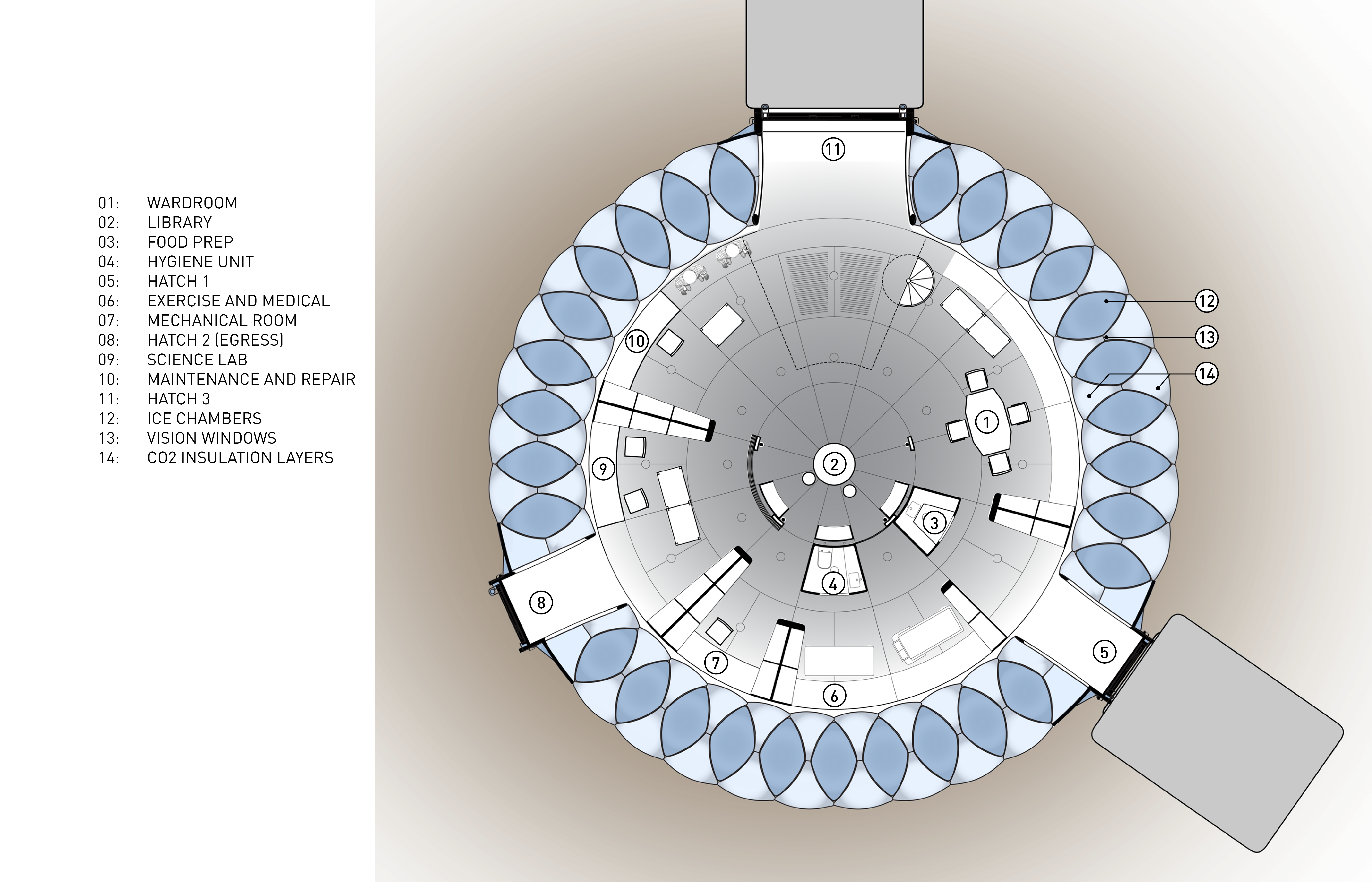
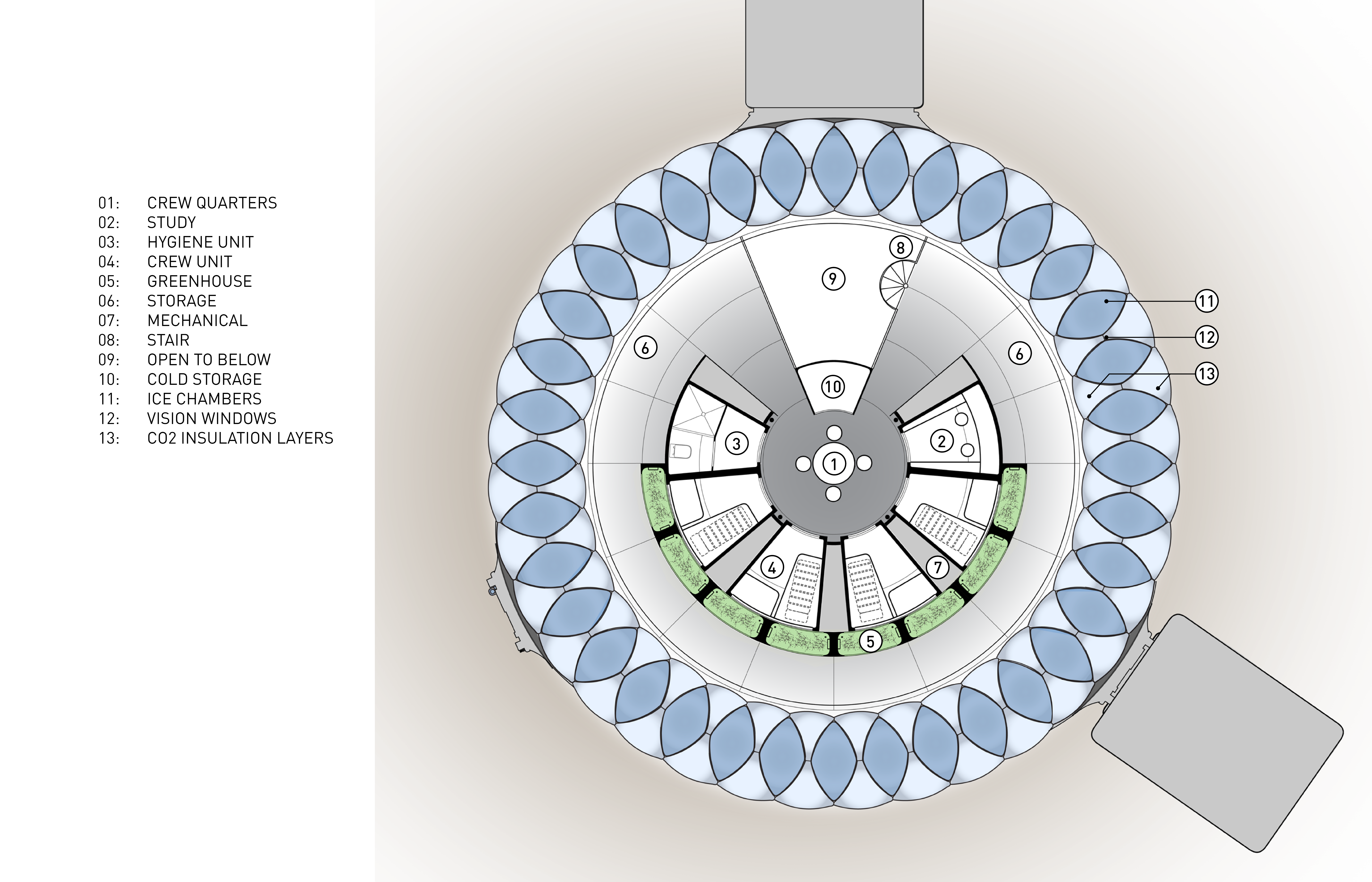
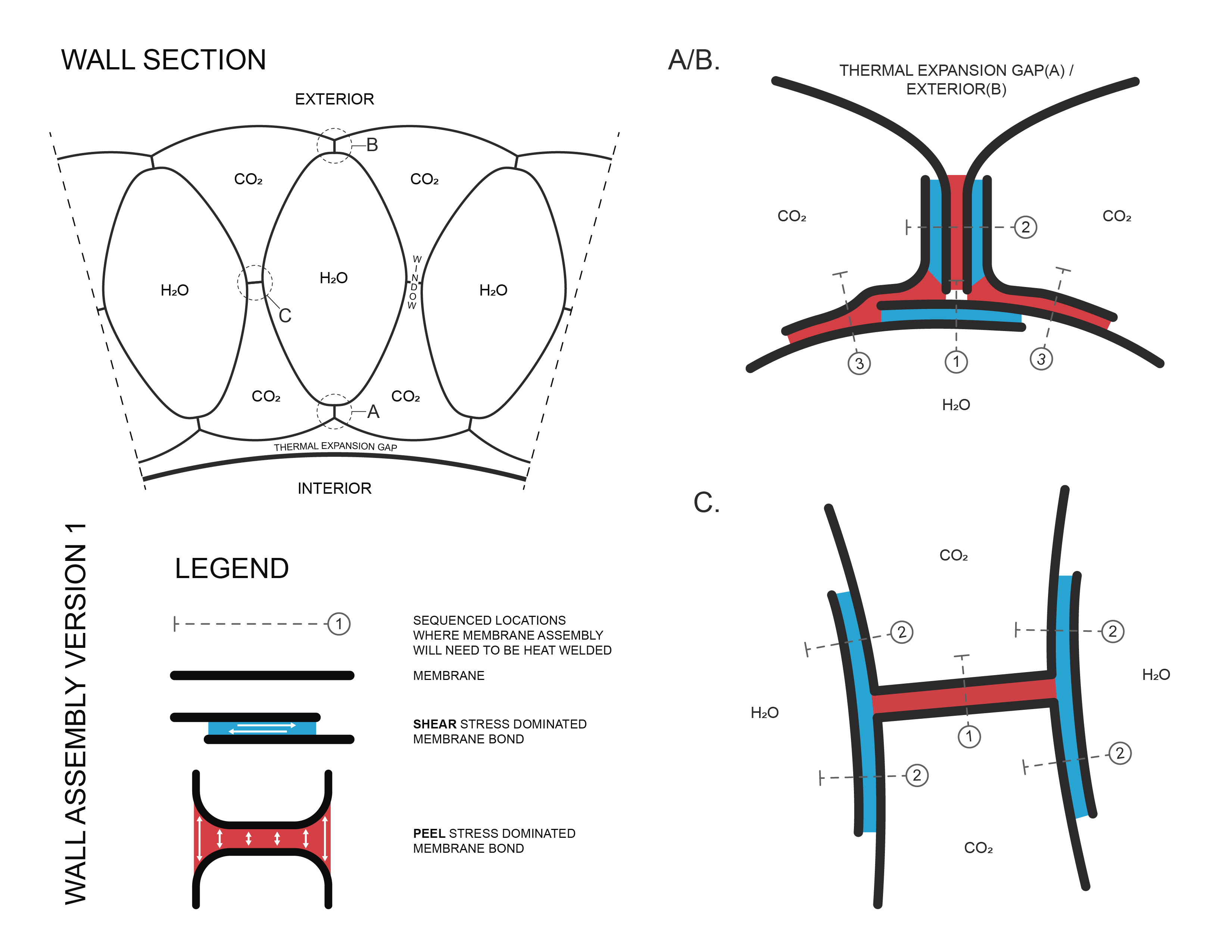
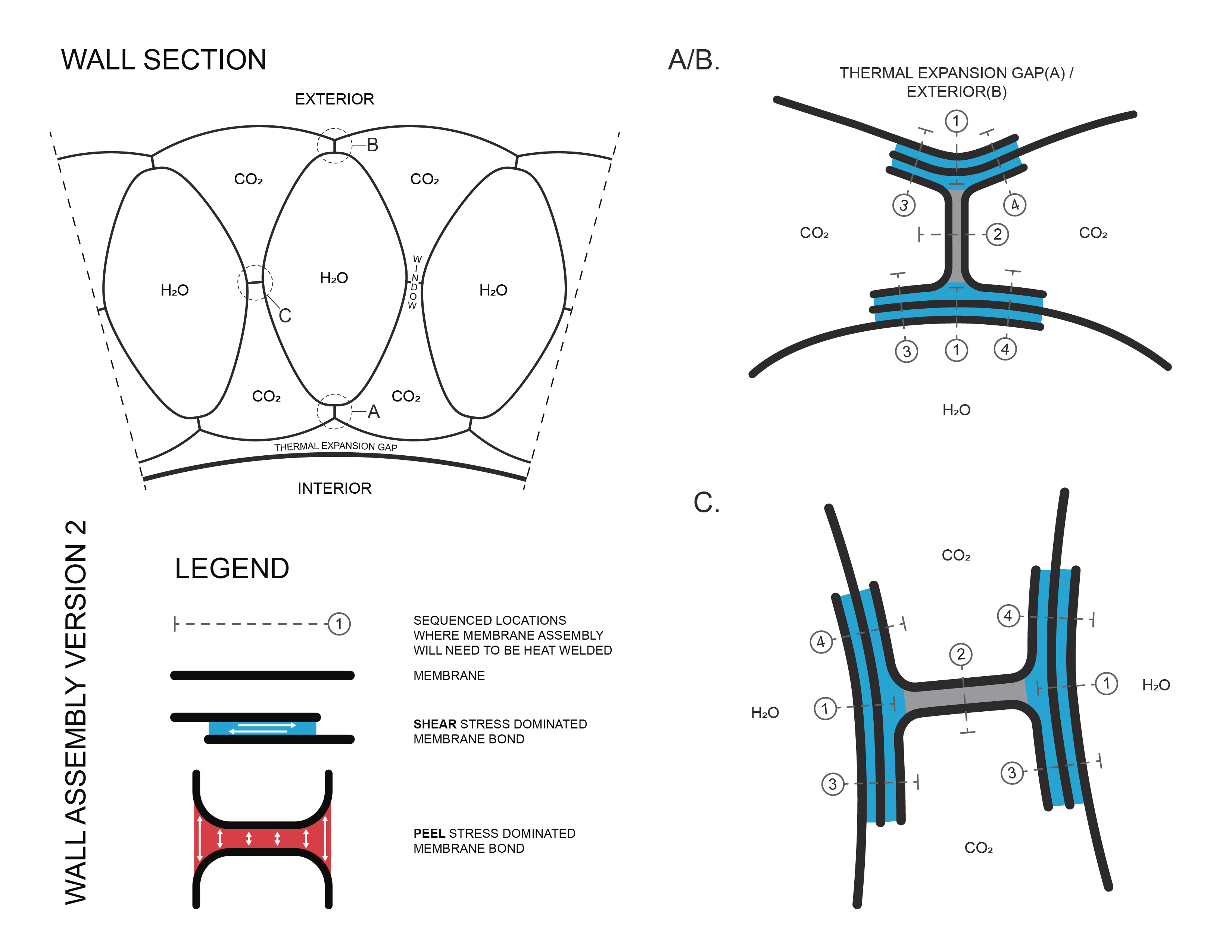
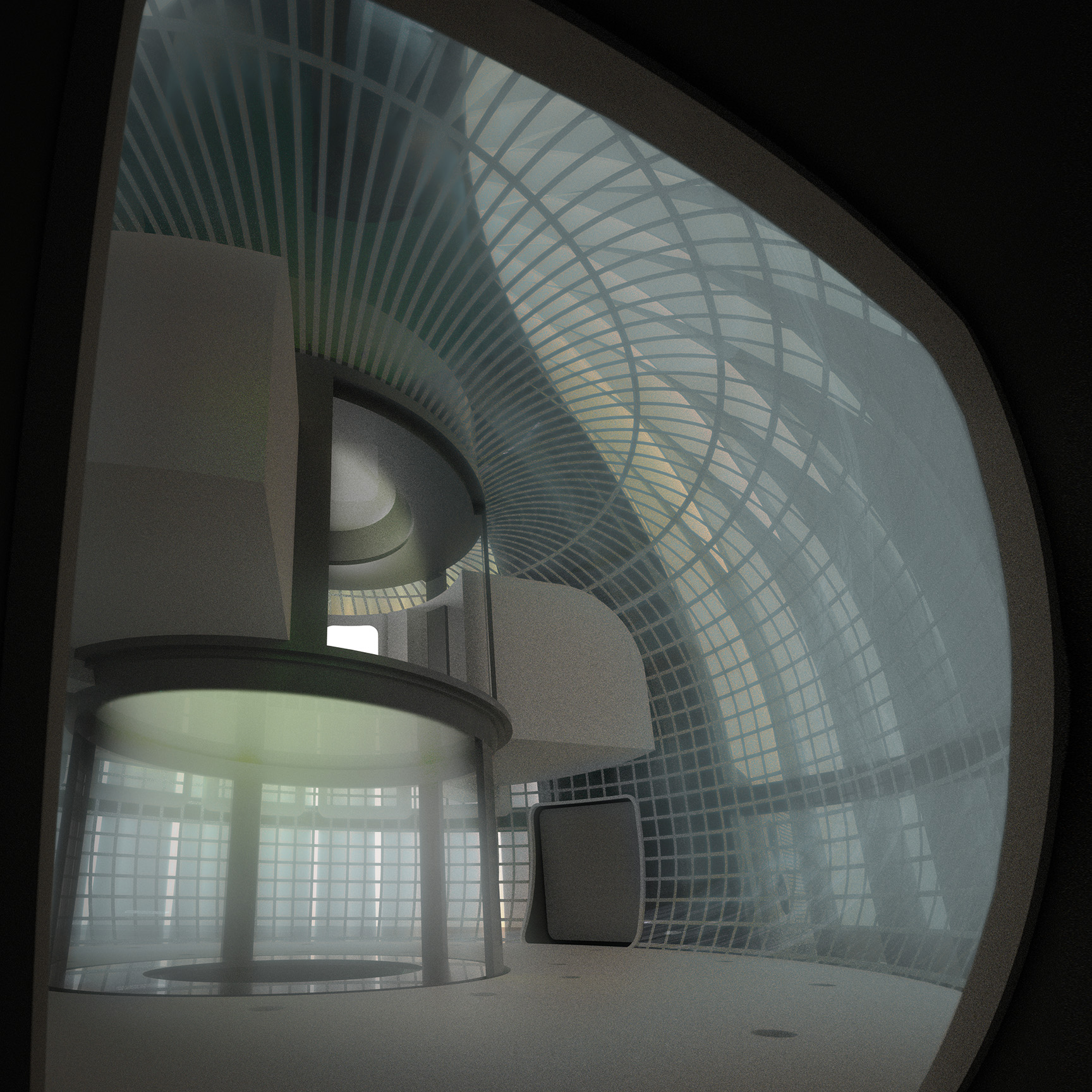
Project Team
Version 1:
NASA (Kevin Kempton, Langley Research Center)
Clouds Architecture Office (Ostap Rudakevych, Masayuki Sono, Yuko Sono, Jeffrey Montes)
SEArch (Christina Ciardullo, Kelsey Lents, Michael Morris, Melodie Yashar)
Version 2:
NASA (Kevin Kempton, Langley Research Center)
Clouds AO (form studies, design, ice cell configuration and sequencing, visualization)
SEArch (fill-freeeze testing, ice mechanics, form studies)
NASA (Kevin Kempton, Langley Research Center)
Clouds Architecture Office (Ostap Rudakevych, Masayuki Sono, Yuko Sono, Jeffrey Montes)
SEArch (Christina Ciardullo, Kelsey Lents, Michael Morris, Melodie Yashar)
Version 2:
NASA (Kevin Kempton, Langley Research Center)
Clouds AO (form studies, design, ice cell configuration and sequencing, visualization)
SEArch (fill-freeeze testing, ice mechanics, form studies)